TM 1-1520-238-10
7A-4
Change 2
Section II.
MAXIMUM TORQUE AVAILABLE
7A.9. DESCRIPTION.
The maximum torque available charts shows the maxi-
mum specification torque available per engine for 30 min-
ute operation (fig 7A-2 sheet 1) and 10 minute operation
(fig 7A-2 sheet 2) at various conditions of pressure altitude
and free air temperature. Both single and dual engine op-
eration limits are shown.
The maximum torque available for 2.5 minute operation
(fig 7A-2 sheet 3) shows the maximum specification
torque available when one engine is inoperative; only
single engine operation limits are shown.
The torque factor charts (figs 7A-3 and 7A-4) provide an
accurate indication of available power for the engines
installed in each individual aircraft.
7A.10. USE OF CHARTS.
The primary use of the maximum torque available charts
(fig 7A-2 sheets 1, 2, and 3) is illustrated by the example.
To determine the maximum specification torque available,
it is necessary to know pressure altitude and free air tem-
perature. Enter the left side of either the 30 minute or the
10 minute chart (fig 7A-2 sheets 1 or 2) at the known tem-
perature and move right to the known pressure altitude,
and then move down and read the maximum specification
torque available. This is torque per engine. For dual en-
gine operation, if the torque per engine exceeds the two
engine limit, the maximum torque available must be re-
duced to the two engine limit.
For one engine inoperative, enter the left side of the 2.5
minute limit chart (fig 7A-2 sheet 3) at the known tempera-
ture and move right to the known pressure altitude, and
then move down and read the maximum specification
torque available for one engine. If the torque exceeds the
one engine limit, maximum torque available must be re-
duced to the one engine limit.
7A.11. CONDITIONS.
The maximum torque available charts (fig 7A-2 sheets 1,
2, and 3) are based on 100% rotor rpm, zero airspeed,
JP-4 fuel and ENG INLET anti-ice switch OFF. With ENG
INLET anti-ice switch ON, available torque is reduced by
as much as 19.3% for 30 minute operation and 18.6% for
10 minute operation. For example, if value from the chart
is 90%, with anti-ice ON, torque available would be 90
19.3 = 70.7%, 30 minute limit.
7A.12. TORQUE FACTOR METHOD.
The torque factor method provides an accurate indication
of available power by incorporating ambient temperature
effects on degraded engine performance. The torque fac-
tor method provides the procedure to determine the maxi-
mum dual or single engine torque available for the en-
gines installed in each individual aircraft. The specification
power is defined for a newly delivered low time engine.
The aircraft HIT log form for each engine provide the en-
gine and aircraft torque factors which are obtained from
the maximum power check and recorded to be used in
calculating maximum torque available.
7A.12.1 Torque Factor Terms.
The following terms
are used when determining the maximum torque available
for an individual aircraft:
a. Torque Ratio (TR).
The ratio of torque available
to specification torque at the desired ambient tempera-
ture.
b. Engine Torque Factor (ETF).
The ratio of an in-
dividual engine torque available to specification torque at
reference temperature of 35 C. The ETF is allowed to
range from 0.85 to 1.0.
c. Aircraft Torque Factor (ATF).
The ratio of an in-
dividual aircrafts power available to specification power at
a reference temperature of 35 C. The ATF is the average
of the ETFs of both engines and its value is allowed to
range from 0.9 to 1.0.
7A.12.2 Torque Factor Procedure.
The use of the
ATF or ETF to obtain the TR from figure 7A-3 for ambient
temperatures between 15 C and 35 C is shown by the
example. The ATF and ETF values for an individual air-
craft are found on the engine HIT log. The TR always
equals 1.0 for ambient temperatures of 15 C and below,
and the TR equals the ATF or ETF for temperatures of 35
C and above.
When the TR equals 1.0 the torque available may be read
directly from the specification torque available scales.
When the TR is less than 1.0, the actual torque available
is determined by multiplying the specification torque avail-
able by the TR (example for TR = 0.98: 90% TRQ X 0.98
= 88.2% TRQ). The torque conversion chart (fig 7A-4) is
provided to convert specification data to actual torque
available. The single and dual engine transmission limits
are shown and should not be exceeded.
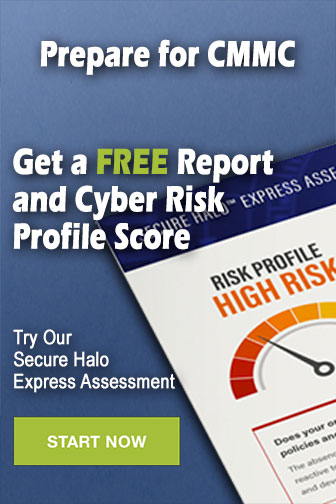