TM 1-1520-238-T-4
419
SECTION II.
THEORY OF OPERATION
47.
SYSTEM DESCRIPTION
47
a. Power Plants.
Power plants (fig. 411) provides power to drive the rotor system. The engines are
mounted in nacelles on the left and right side of the helicopter and drive the rotors through the NGBs. Access to
the engines is through a work platform that is a part of each nacelle. The engines are easily configured for
installation on either side of the helicopter. Engine cooling air is drawn from the main transmission deck into the
nacelle by the jetpumping action of the primary nozzle and the exhaust system while cooling doors in each
nacelle open and close automatically. A history recorder records and displays the engine operating hours,
time/temperature index, and low cycle fatigue (LCF) events. The engine bleed air subsystem provides fifth stage
compressor bleed air for the antiice system and PAS. Provisions for water wash of the engines are also
provided.
(1) The pilot and CPG power quadrants are connected together with flexible control cables which transmit
power selections from the power levers to the HMU torque motor on the engine. Control inputs to the HMU are
also received from the collective sticks. The pilot power quadrant provides engine start controls and indicators and
a rotor brake switch. The CPG power quadrant provides an emergency hydraulic power switch and a battery
override switch.
(2) The engine starter is pneumatically operated and rotates the compressor through the accessory
gearbox until the engine reaches a speed that permits it to be selfsustaining. The engine exciter and igniter plugs
supply high voltage sparks to ignite the fuel during engine starting.
(3) An oil pressure transducer is installed on each engine to drive the engine oil pressure indicator. An oil
filter bypass sensor measures differential pressure across the oil filter and lights the OIL BYP ENG 1 or OIL BYP
ENG 2 indicator on the pilot caution/warning panel and the ENG 1 or ENG 2 indicator on the CPG caution/warning
panel. Each engine is equipped with a chip detector system to detect metal particles in the oil system and lights
the CHPS ENG 1 or CHPS ENG 2 indicator on the pilot caution/warning panel and the ENG 1 or ENG 2 indicator
on the CPG caution/warning panel. A monopole permanent magnet pickup monitors engine rpm and sends the
signal to the ECU or DECU. Turbine gas temperature (TGT) is sensed by chromelalumel sensors on the TGT
harness and displayed on the TGT indicator. A fuel filter bypass sensor measures differential pressure across the
fuel filter and lights the FUEL BYP ENG 1 or FUEL BYP ENG 2 indicator on the pilot caution/warning panel and
the ENG 1 or ENG 2 indicator on the CPG caution/warning panel. The engine out warning unit provides visual and
audible warning when main rotor or engine rpm is low.
b. Purpose.
Power plants provides power to operate the drive systems on the helicopter.
c. System Operation.
Refer to TM 55-2840-248-23 for operation of power plant, fuel, oil, air and electrical
systems. Related subsystems (described here) control the engines and provide engine cooling and exhaust. The
subsystems include the engine cooling, engine exhaust, engine antiice, engine ignition (starting), engine power,
and control and indicators.
(1) Engine Cooling Subsystem.
The engine cooling subsystem provides cooling air for the engines
during and after operation. The cooling and exhaust systems work together. The exhaust system helps the cooling
airflow, the engine cooling air cools the exhaust gases and components.
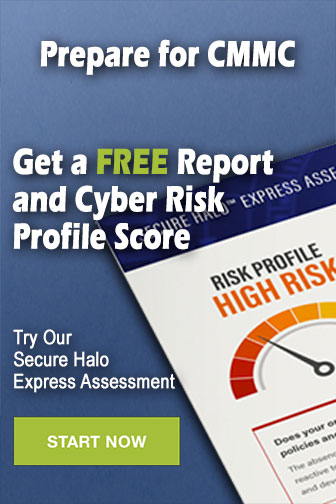