TM 1-1520-238-T-7
117
112.
LOCATION AND DESCRIPTION OF MAJOR COMPONENTS (cont)
112
(6) Collective Servocylinder.
The collective servocylinder, mounted on the transmission deck just left of
the centerline and forward of the transmission, provides hydraulic power to assist movements of upper and lower
controls. The collective servocylinder receives inputs from either the mechanical controls or electrical components
(BUCS and DASE) which cause hydraulic pressure to move the cylinder piston.
(7) Mixer Assembly.
The mixer assembly, mounted above the main rotor support structure base
assembly, receives and combines control inputs from the collective and cyclic sticks for vertical, longitudinal and
lateral flight of the helicopter. The collective bellcrank is a component of the mixer assembly and is attached to the
collective servocylinder, support bearings, lateral and rear longitudinal bellcrank. It is horn shaped, with the horns
facing aft.
(8) Lateral Links.
Two lateral links, mounted between the mixer assembly and the swashplate assembly,
provide vertical and lateral control of the stationary swashplate by inputs received from the collective and cyclic
sticks.
(9) Torque Link.
The torque link, mounted between the mixer assembly and the swashplate assembly,
provides vertical and longitudinal control of the stationary swashplate by inputs received from the collective and
cyclic sticks.
(10) Swashplate Assembly.
The swashplate assembly, mounted on the static mast between the mixer
assembly and the main rotor head assembly, receives and transmits control inputs from the collective and cyclic
sticks to the main rotor head assembly. The swashplate assembly consists of a stationary swashplate, a rotating
swashplate, a self-aligning spherical and slider bearing (uniball) and a bearing assembly (double-roll ball bearing).
Collective input raises or lowers the swashplate assembly, equally changing the angle of attack of the four main
rotor blades.
(a) The stationary swashplate, mounted to the double-roll ball bearing assembly below the rotating
swashplate, supports the swashplate assembly and receives control inputs from two lateral links and a torque link.
It houses the self-aligning spherical and slider bearing, and attaches to the inner race of the double-roll ball
bearing assembly.
(b) The rotating swashplate, mounted to the double-roll ball bearing assembly above the stationary
swashplate, transmits control inputs received from the stationary swashplate to the main rotor head assembly via
the pitch link assemblies. The rotating swashplate is an aluminum forging with four clevis lugs 90 apart for
attachment of the pitch link assemblies. Two of the clevis lugs (180 apart) have attachment pins for two scissor
assemblies. The rotating swashplate houses the outer race of the double-roll ball bearing assembly.
(c) The bearing assembly, located between the stationary and rotating swashplate, allows the rotating
swashplate to rotate. It is a double-roll ball bearing assembly with a one-piece outer race and a three-piece inner
race, with flexible and removable upper and lower seals.
(d) The self-aligning spherical and slider bearing (uniball), located between the stationary and rotating
swashplate, allows the swashplate assembly to tilt for cyclic control movements. The slider bearing allows the
entire swashplate assembly to move the static mast up or down as a unit for collective control movements. The
upper and lower bearing retainers secure the self-aligning spherical and slider bearing and the double-roll ball
bearing assembly. The upper bearing retainer mounts to the stationary swashplate. The lower bearing retainer
mounts to the rotating swashplate.
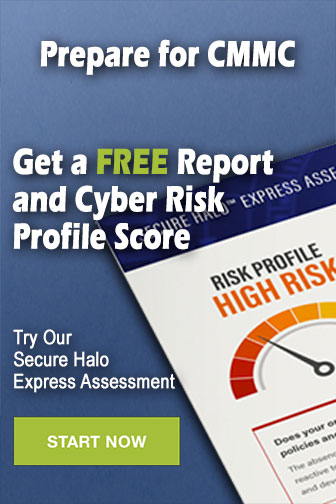