TM 1-1520-238-23
1-158.2
Change 9
1.49.
CORROSION CONTROL/INSPECTION continued
d. Crevice
Crevice corrosion occurs when the electrolyte has a different concentration from one area to another. This type of
corrosion is also known as concentration cell corrosion. Electrolyte inside the crevice contains less oxygen and more
metal ions than electrolyte just outside the crevice. As a result, the metal surfaces, even though they may be part of
the same metal, than have different activities and corrosion occurs inside the crevice. This kind of corrosion also
occurs when a surface is covered by a foreign material. There are three general types or crevice corrosion: (1) metal
ion concentration cells, (2) oxygen concentration cells, and (3) active-passive cells.
e. Intergranular
Intergranular corrosion is an attack on the grain boundaries of the metal. It consists of quantities of individual grains,
each having a clearly defined boundary, which chemically differs from the metal within the grain. Frequently the grain
boundaries are anoxic to the metal within the grain. When in contact with an electrolyte, rapid corrosion occurs at the
grain boundaries.
f. Exfoliation
Exfoliation is an advanced form of intergranular corrosion where the surface grains of a metal are lifted up by the
force of expanding corrosion products occurring at the grain boundaries. The lifting up or swelling is visible evidence
of exfoliation corrosion. Exfoliation occurs on extruded, rolled, wrought, and forged high strength aluminum and
magnesium parts.
g. Filiform
Filiform corrosion is a special form of oxygen concentration cell corrosion or crevice corrosion which occurs on metal
surfaces having an organic coating system. It is recognized by its characteristic wormlike trace for corrosion
products beneath the paint film. Filiform occurs when the relative humidity or the air is between 78 percent and 90
percent, and when the surface is slightly acidic. It starts at breaks in the coating system, such as scratches and
cracks around fasteners and seams, and proceeds underneath the coating, due to the diffusion of water vapor and
oxygen from the air through the coating. Filiform corrosion can attack steel, magnesium, and aluminum surfaces and
may lead to more serious corrosion in some locations. Filiform corrosion can be prevented by storing equipment and
aircraft in an environment with a relative humidity below 70 percent, by using coating systems having a low rate of
diffusion for oxygen and water vapors, by maintaining coatings in good condition, and by washing equipment and
aircraft to remove acidic contaminants from the surface. Maintain coatings in good condition and apply corrosion
preventive compounds when paint is damaged.
1.49.8. Corrosion and Mechanical Factors
a. Stress corrosion cracking is the intergranular cracking of a metal caused by the combined effects of constant
tensile stress (internal of applied) and corrosion. Internal or residual stresses are produced by cold working, forming,
and heat treatment operations during manufacture of a part and remain concealed in the part unless stress relief
operations are used. Other hidden stresses are induced in parts when press or shrink fits are used and when slightly
mismatched parts are clamped together with rivets and bolts. All these stresses add to those caused by applying
normal loads to parts during operation. Metals have threshold stresses below which stress corrosion cracking will
not occur. This threshold stress which varies from metal to metal, is different for different tempers of the same metal,
and is different for each of the three directions in which stress can be applied.
GO TO NEXT PAGE
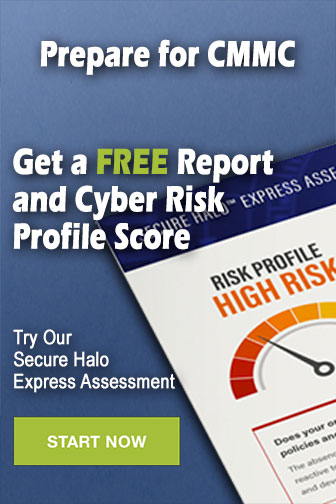