TM 1-1520-238-23
Change 9
1-158.3
1.49.
CORROSION CONTROL/INSPECTION continued
b. Associated hazards. Stress corrosion cracking is an extremely dangerous type of failure because it can occur
at stress levels far below the rated strength of a metal, starting from what is thought to be a very minor corrosion pit.
Parts can completely sever in s split second or they can crack slowly, and the rate of cracking is very unpredictable
in operating service.
c. Causes. Specific environments have been identified which cause stress corrosion cracking of certain alloys.
Salt solutions, sea water, and moist, salt-ladden air may cause stress corrosion cracking of heat-treatable aluminum
alloys, stainless steels, and some titanium alloys. Magnesium alloys may stress corrode in moist air. Stress
corrosion can be prevented by placing an insulating barrier between the metal and the corrosive environment by
applying protective coatings and water displacing corrosion preventive compounds. Stress relief operations during
fabrication of parts will help, because it lowers the stress level on the parts. Shot peening a metal increases
resistance to stress corrosion cracking by creating compressive stresses on the surface, which must be overcome
by an applied tensile stress before the surface sees any tension load.
d. Corrosion fatigue is the cracking of metals caused by the combined effects of cyclic stress and corrosion, and
is very similar to stress corrosion cracking. No metal is immune to some reduction in its resistance to cyclic stressing
if the metal is in a corrosive environment. Damage from fatigue corrosion is greater than the sum of the damage from
both cyclic stresses and corrosion. Corrosion fatigue failure occurs in two stages. During the first stage, the
combined action of corrosion and cyclic stress damages the metal by pitting and crack formation in the pitted area.
The second stage is the continuation of crack propagation by a straight fatigue mode, in which the rate of cracking
is controlled by: (a) stress concentration in the main cross section, and (b) the physical properties of the metal.
Fracture of metal part due to fatigue corrosion occurs at a stress far below the fatigue limit, even though the amount
of corrosion is unbelievably small. For this reason, protection of all parts subject to alternating stress is particularly
important, even in environments that are only mildly corrosive. Preventive measures are the same as those given for
stress corrosion cracking as stated above.
e. Fretting corrosion is special form of concentration cell corrosion, which occurs in combination with surface
wear. The corrosion products increase the wear of the surface and the wear exposes more bare metal surface to be
corroded. The overall effect is greater than the single effects of corrosion and wear added together. It has the general
appearance of galling, in which chunks of metal are torn from the surface, with corrosion at the torn areas or ragged
pits. This type of corrosion occurs on faying surfaces of close tolerance and on parts under high pressure in a
corrosive environment when there is slight relative movement of the parts, such as that caused by vibration.
1.49.9. Corrosion and Composites
Composite materials do not corrode; however, they may accelerate corrosion on adjacent metal structures and
attaching hardware due to galvanic effect. Graphite composites are made from carbon fibers which are electrically
conductive, and one of the noble metals (gold, silver, mercury, platinum, palladium, iridium, and etc.) materials in the
galvanic series. Special precautions must be exercised when metal parts are present with composite parts. Also
many composites parts may have metal sandwiched between layers or composite at edges, holes, and attaching
points. These metals, if exposed, may corrode and cause delamination.
GO TO NEXT PAGE
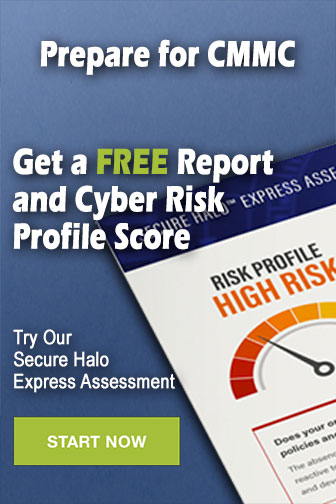