TM 1-1520-238-23
6-10
Change 9
6.1.
DRIVE SHAFT INSPECTION continued
f. Check No. 4 and No. 5 tail rotor drive shaft with nickel plated wear sleeves for movement and broken
paint stripe.
(1) Perform both initial and recurring inspection after aircraft has been in coolest possible ambient tempera-
ture for 30 MINUTES or more.
(2) Check for broken paint stripe on all four wear sleeves. If broken paint stripe is detected check wear sleeves
for damage or movement per the following steps. If no damage or movement is found, reapply paint stripe.
(3) Locate two wear sleeves attached to No. 4 and No. 5 tail rotor drive shaft. Wear sleeves are located within
damper and anti-flail supports. For wear sleeves located within anti-flail supports, remove anti-flail sup-
ports and support brackets from tailboom and slide anti-flail supports forward far enough to obtain an
unobstructed view of wear sleeve (para 6.8 and para 6.11).
(4) While preventing drive shaft movement, attempt to move all four wear sleeves attached to drive shaft in
both axial and radial direction. One person holds drive shaft and other attempts to move wear sleeves. If
any of wear sleeves rotate with respect to shaft or have horizontally displaced down shaft, replace tail rotor
drive shaft(s) (para 6.8 and/or para 6.11).
(5) Wear sleeve distress, which does not penetrate the nickel plating (0.001-0.002 INCH thick), is acceptable.
Check wear sleeves for rust or exposed base metal (missing nickel plating). If detected, replace tail rotor
drive shaft(s) (para 6.8 and/or para 6.11).
(6) Check diameter of wear sleeves. If wear sleeve is less than 4.740 INCHES in diameter, replace tail rotor
drive shaft(s) (para 6.8 and/or para 6.11).
(7) Install anti-flail supports on tailboom (para 6.8 and para 6.11).
(8) Check for scratches through nickel. None allowed.
g. Check No. 4 and No. 5 tail rotor drive shafts with black hard coat aluminum wear sleeves.
(1) Wear sleeve surface distress such as scratches, pits, nicks, etc. are acceptable up to a maximum depth of
0.010 INCH. If surface distress exceeds this limit, replace tail rotor drive shaft(s) (para 6.8 and/or para
6.11).
(2) Check diameter of wear sleeves. If wear sleeve is less than 4.740 INCHES in diameter, replace tail rotor
drive shaft(s) (para 6.8 and/or para 6.11).
h. Check couplings, flanges, and diaphragms for cracks.
(1) Use magnifier where needed. Clean suspected areas with brush (item 34, App F) and methyl ethyl ketone
(item 124, App F). Check with fluorescent inspection kit (TM 55-1500-335-23).
(2) Check for elongated bolt holes, bends or abrasions. None allowed. Use brush (item 34, App F) and methyl
ethyl ketone (item 124, App F). Discard brush in suitable container.
i. Check diaphragms for nicks, scratches, dents, flaking paint, or distortion. None allowed.
j. Check coupling flanges for peeling or other failure of aluminum bronze (plasma) coating.
(1) Check aluminum-bronze (plasma) coating for gouges, nicks, and/or scratches. Minor nicks, gouges, and
scratches can be blended out; however, damage through coating to bare metal is not allowed. Damage
cannot exceed 20 PERCENT of surface area.
(2) Check for peeling of aluminum-bronze (plasma) coating. None allowed.
(3) Discoloration due to oxidation or minor chipping around bolt holes is acceptable.
GO TO NEXT PAGE
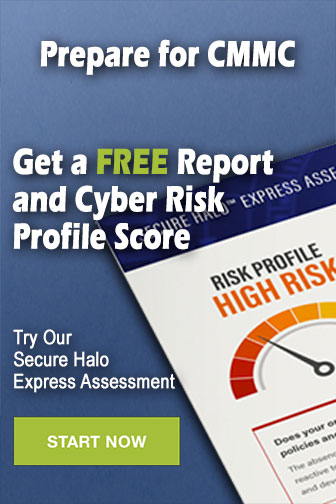