TM 1-1520-238-T-5
Change 6
729
77.
SYSTEM DESCRIPTION (cont)
77
(b) The utility hydraulic manifold (fig. 713) has two modes of operation, normal and GSE. During
normal operation, pressurized air (30 5 psi) from the PAS manifold enters through a oneway air inlet check
valve. The pressurized air acts upon the reservoir piston creating a low pressure hydraulic fluid and helps prevent
pump cavitation. The air relief valve protects the air pressure side by opening at 105 psi. The low pressure relief
valves open at 215 psi, relieving excess trapped fluid and air. A manual air bleed valve is used to relieve reservoir
air pressure during maintenance. When the reservoir reaches the lowest permissible fluid level volume, the low
level switch closes. A low level valve is actuated causing all auxiliary functions to be turned off hydraulically. The
low level switch lights the pilot caution/warning panel OIL LOW UTIL HYD indicator and actuates the emergency
hydraulic control valve. Low pressure fluid is drawn by pump suction to the utility hydraulic pump, pressurized to
3000 psi, and returned to the utility hydraulic manifold. High pressure entering the utility hydraulic manifold is
sensed by the pressure switch. When pressure rises above 2050 psi the pressure switch opens and extinguishes
the pilot PRI UTIL PSI indicator and the CPG UTIL HYD indicator on the respective caution/warning panels. The
pressurized fluid is filtered by a five micron filter. If the filter is partially clogged, the differential pressure of 70 10
psi is sensed by an electrical switch in the dirty filter indicator. The switch closes, causing the OIL BYP UTIL HYD
indicator on the pilot caution/warning panel to light and extends a popup visual indicator on the utility hydraulic
manifold (the pressure filter has no bypass capabilities). Fluid is isolated from the GSE ports during normal
operation by the GSE check valve. A high pressure relief valve returns excessive pressure to the return side of
the utility hydraulic manifold. The accumulator isolation inlet valve and the accumulator isolation valve isolate
accumulator pressure in the accumulator and utility hydraulic manifold. When the helicopter is shutdown, the
accumulator isolation valve opens, dumping accumulator pressure when the rotor head is rotated in the normal
direction. The hydraulic pump pressurizes fluid to cause the opening of the valve. Fluid going through the
accumulator isolation inlet valve is replenished after an APU start and pressurized to 3000 psi. Rotor brake
solenoid S1 is energized by the pilot power quadrant RTR BK switch when set to BRAKE position. Opening of the
solenoid permits 3000 psi into the brake circuit. With solenoid S2 closed, the brake metering valve permits 337
25 psi pressure to be routed to the rotor brake actuator. A rotor break pressure switch actuates a throttle lock
relay and lights the pilot caution/warning panel RTR BK indicator. The power lock relay prevents the power levers
from being advanced past the IDLE position. The override solenoid is opened by the pilot instrument panel EMER
HYD switch and the CPG power quadrant EMER HYD PWR switch. When opened, the solenoid routes
accumulator pressure to open the accumulator isolation valve, permitting use of emergency power to the utility
side of the servocylinders. The emergency transducer transmits the amount of pressure available to the UTIL
ACC indicator. The pilot EMER HYD and CPG EMER HYD PWR switches are also used to deplete accumulator
pressure before maintenance on the utility system, except when removing and replacing manifold or servocylinder
filters. Prior to output to the flight control servocylinders, fluid pressure is monitored by the pressure transducer.
The pressure transducer provides signals to the UTIL side of the pilot dual hydraulic pressure indicator. Pressure
from the pump to the accumulator isolation valve goes through the auxiliary isolation valve to flight controls. Fluid
returning from the flight control servocylinders is filtered by a five micron filter. If the filter is partially clogged, the
differential pressure of 70 10 psi is sensed by an electrical switch in the dirty filter indicator. The switch closes,
causing the OIL BYP UTIL HYD indicator on the pilot caution/warning panel to light and extends a popup visual
indicator in the primary hydraulic manifold. A differential pressure of 100 15 psi, a bypass valve opens and allows
the unfiltered fluid to be routed around the return filter to the primary hydraulic manifold. After being filtered, the
fluid returns to the pump. The APU return port routes fluid from the APU through a system return filter screen into
the utility hydraulic reservoir.
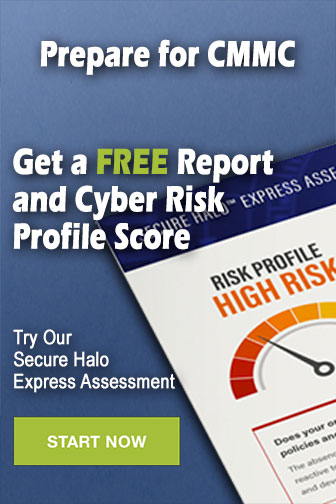