TM 1-1520-238-23
Change 4
2-94.1
2.34.
ELECTROMAGNETIC CONDUCTIVE COATING APPLICATION continued
b. Apply conductive coating. Use corrosion resistant coating (item 65, App F).
NOTE
Paint shall be applied with a pressure of 10 to 20 PSI. It is important to agitate paint mixture every 2 to
3 minutes to keep the conductive fillers suspended in the paint solution.
(1) Spray one uniform coat of corrosion resistant coating (item 65, App F) to a thickness of 2.00 to 4.00 MILS.
Use spray gun.
(2) Check coated surface for correct thickness (TM 55-1500-345-23).
c. Inspect (QA).
d. Remove tape.
WARNING
Do not place heater near flammable material or allow heater to contact skin: severe burns can
result. Wear protective equipment. If injury occurs, seek medical aid.
e. Cure conductive coating.
NOTE
Conductive coating will cure tack free in 4 HOURs at room temperature. Conductive coating will
obtain 90% of coatings properties within 24 HOURS.
A minimum of 7 DAYS is required for conductive coating to cure at room temperature before coating
obtains electrical properties.
(1) Force curing may be accomplished by the following methods:
(a) Cure composite parts 4 HOURS at room temperature. Then heat 4 HOURS at 130 F (54 C). Use
heater.
(b) Cure aluminum parts 4 HOURS at room temperature. Then heat 1 HOUR at 250 F (121 C). Use
heater.
(2) Perform electrical resistance check on surface (TM 55-1500-323-24). The surface resistance reading shall
be 1.00 OHM or less.
(a) Place electrical leads 1 inch apart on conductive coating. If surface resistance exceeds 1.00 OHM,
re-coat surface. Use multimeter.
f. Inspect (QA).
GO TO NEXT PAGE
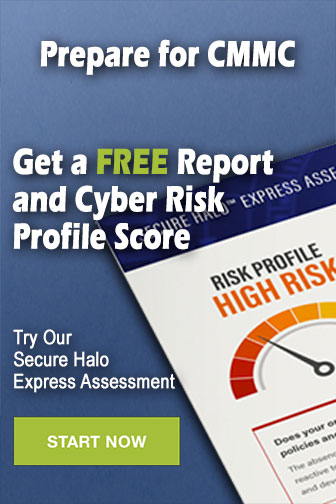