TM 1-1520-238-23
Change 4
2-95
2.34
ELECTROMAGNETIC CONDUCTIVE COATING APPLICATION continued
(8) Mask areas adjacent to surface to be coated with conductive coating. Ensure that surrounding areas are
protected from drips or over-spray.
NOTE
Conductive coating must be thoroughly mixed before combining due to high conductive filler
content. The mix ratios shall be in accordance with the manufacturers instructions.
Coating material shall be thinned in accordance with the manufactures instructions for spraying or
brushing. The coating shall be within 2 HOURS after mixing.
Brush application of the conductive coating should be limited to minor touch-up repairs. The E.M.I.
properties of the paint may be reduced, due to surface irregularities caused by brushing.
If brush application of the conductive coating is required, go to step (9). If spray applications of the
conductive coating is required, go to step (11).
(9) Brush application: Brush the surface with conductive coating material. Overlap edge of damaged area
approximately 0.75 INCH where possible (first pass should completely wet the surface). Allow 2 to 10
MINUTES before re-painting to complete the first coat. Dry for 30 MINUTES to 2 HOURS before applying
a second coat. Use brush (item 36, App F) and corrosion resistant coating (item 65, App F).
(10) Apply a second coat of conductive coating. Use corrosion resistant coating (item 65, App F). Proceed to
step (12).
NOTE
Paint shall be applied with a pressure of 10 to 20 PSI. It is important to agitate paint mixture every 2 to
3 minutes to keep conductive fillers suspended in the paint solution.
(11) Spray application: Apply a uniform coat of conductive coating by spraying four to five even passes over
component surface from a distance of 6 to 10 INCHES. Use corrosion resistant coating (item 65, App F).
(12) Apply curing criteria in paragraph 2.34.4.e.
b. Inspect (QA).
GO TO NEXT PAGE
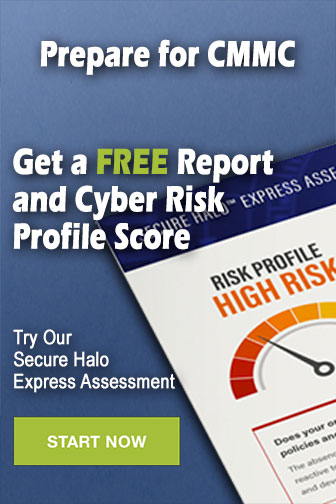