TM 1-1520-238-23
6-502
Change 5
6.121.
INTERMEDIATE GEARBOX INSPECTION continued
(3) Check studs for crossed, stripped, or flattened threads. None allowed.
(a) Locking serrations flush to below surface of housing. No looseness allowed.
(4) Check thread holes for crossed, stripped, or flattened threads. None allowed.
(5) Check inserts for loose, crossed, stripped, or flattened threads. None allowed. Top of insert flush to below
surface of housing.
(6) Check mounting holes for a maximum diameter of 0.430 INCH. Use caliper.
(7) Check housing for dings and nicks not to exceed 0.050 INCH before blending. Use depth gage.
(a) After blending, magnesium must be corrosion protected (para 1.49).
e. Check temperature sensors for cracked, broken, or burned insulation.
(1) Check for secure splices to gearbox harness.
f. Check retainers for serviceability.
(1) Check for fractures and/or cracks. None allowed. Use fluorescent inspection kit (TM 55-1500-335-23).
NOTE
The eddy current inspection method is an alternate method for identifying cracks. If a crack in the
intermediate gearbox retainers is suspected, refer to TM 1-1520-264-23.
(2) Check clinch nuts for crossed, stripped, or flattened threads. None allowed. Top of serrations flush to below
surface of housing. No looseness allowed.
(3) Maximum diameter of bolt holes 0.330 INCH. Use caliper.
(4) Check for nicks, gouges, burrs, and corrosion not deeper than 0.040 INCH before blending, except for
specific surfaces. Use depth gage.
(a) Check mounting surface for damage and/or corrosion, not deeper than 0.020 INCH before blending
and not over 25 percent of total area. Not more than 10 percent damage in one localized area. Use
depth gage.
(5) Check packing groove for damage. None allowed.
g. Check gearbox flange or shouldered shaft for serviceability.
(1) Check for nicks, burrs, gouges, and corrosion. Except for surfaces identified below, depths less than 0.020
INCH before blending are acceptable. Use depth gage.
(2) Check for fractures and cracks. None allowed.
GO TO NEXT PAGE
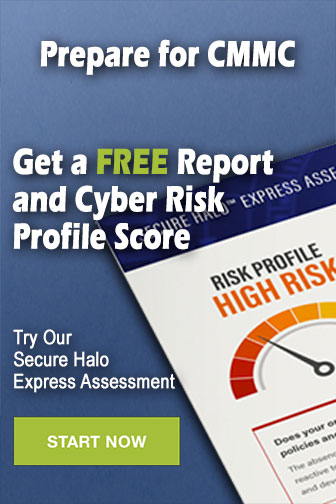