TM 1-1520-238-23
6-548
Change 9
6.132.
TAIL ROTOR GEARBOX INSPECTION continued
c. Tail rotor gearbox inspection for grease leakage.
(1) Check gearbox for evidence of grease leakage from gearbox at static seams and joints. None allowed.
(2) Check for evidence of grease leakage at input seal.
(a) Seepage of grease is not cause for concern.
(b) If evidence of grease exists, wipe off purged grease.
(c) If new grease leakage is observed in excess of 1 OUNCE (approximately 33 drops) during standard 10
hour and/or 14 day maintenance inspection, replace seal (para 6.135).
(3) Check for evidence of grease leakage at output seal.
(a) Seepage of grease is not cause for concern.
(b) Initially 1/2 ounce of grease (approximately 15 drops) is expected to be purged and is required to
lubricate lip sealing surface.
(c) If evidence of initial grease is observed, wipe or wash away purged grease with alcohol. Use caution
not to push grit-filled grease in lip seal which could cause it to be cut and wear at an excessively high
rate. Use alcohol (item 25, App F).
(d) At next standard 10 hour and/or 14 day inspection interval, examine output seal for evidence of new
grease leakage. Eddy current inspection method is an alternate method for finding cracks. If crack in
tail rotor gearbox pinion input and output retainers is suspected, refer to TM 1-1520-264-23 for
non-destructive inspection procedure.
(e) If amount of grease purged is sufficient to collect at base of static shaft and form a drop, remove
gearbox.
d. Check tail rotor gearbox housing, and pinion gear input and output retainers for cracks. None allowed.
Use magnifier where needed.
(1) Clean suspected areas. Use brush (item 34, App F) and methyl ethyl ketone (item 124, App F).
(2) Check for fractures and/or cracks. None allowed. Use fluorescent inspection kit (TM 55-1500-335-23).
e. Check temperature sensors for cracked, broken, or burned insulation.
(1) Check for secure splices to gearbox harness (para 6.138).
GO TO NEXT PAGE
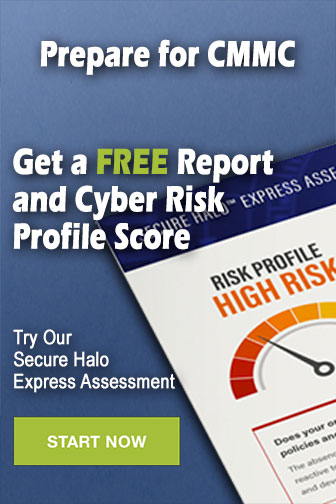