TM 1-1520-238-23
7-14.2
Change 9
7.2.
HYDRAULIC SYSTEM LEAK CHECK
(23) Flush is complete.
(24) If required, perform bleed in accordance with TM 1-1520-238-23, paragraph 1.35, or TM 1-1520-Longbow/
Apache (IETM).
NOTE
The Y hoses in mentioned paragraph 1.35 will be replaced with the dual hydraulic manifold. The
Y hoses will be an authorized substitute if the dual hydraulic manifold is not available. To drain the
aircraft when using the Y hose, disconnect the return line at the AGPU and allow the hydraulic fluid
to drain into a 10 (ten) gallon bucket.
(25) Switch AGPU hydraulic output to OFF and decrease hydraulic pressure to 500 PSI. Switch hydraulic
power to OFF.
(26) While monitoring utility manifold reservoir level, move return/bypass to bypass position until proper reser-
voir level is reached, then switch back to OFF position.
(27) Shut down AGPU. Disconnect and store hoses and manifold.
(28) Perform primary and utility hydraulic MOC in accordance with TM 1-1520-238-t or TM 1-1520-Longbow/
Apache (IETM).
7.2.5. Hydraulic Fluid Sampling Inspection.
a. General Instructions for taking proper hydraulic fluid samples of AGPU and aircraft.
(1) Use 3-ounce AOAP plastic oil sample bottle (item 31A, App F) to collect samples.
(2) Remove dirt and other external contaminants from sampling point and all hardware connections by rinsing
with cleaning solvent (item 45, App F) or equivalent environmental preferred solution and wipe dry with
lint-free cloth.
NOTE
Sampling points, hoses, and connections that have not been adequately cleaned prior to use may
produce erroneous test results and needless rejection of the systems under test.
NOTE
Prior to taking the sample, operate the system being tested for the amount of time necessary to
obtain a representatie system contamination level (15-30 minutes).
(3) Initiate flow of fluid to be sampled by whatever means appropriate; allow initial quantity (approximately 3
ounces) to flow into waste receptacle. This procedure serves to flush away any contaminants in sampling
line and any contaminants generated by mechanical operations.
(4) Without interrupting flow of fluid, place clean 3-ounce AOAP oil sample bottle under fluid stream and fill
bottle partially (approximately 1/4 inch from bottom). Stop flow.
GO TO NEXT PAGE
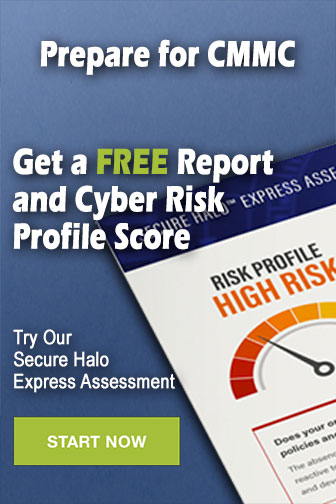