TM 1-1520-238-T-4
Change 9
563
524.
ISOLATING/MONITORING OTHER VIBRATIONS USING AVA EQUIPMENT (cont)
524
Spectrums
What is a spectrum? If you mount an accelerometer on a particular point on an airframe, a spectrum will show
how that point is responding to the forces generated by the rotating components of the helicopter. A peak at a
particular frequency associated with a rotating part is the amplitude of the response, the vibration of that point to
the forces generated by that part. The higher the peak the more forces that part is generating. Low frequency
vibrations come from the rotors. Mid frequency vibrations come from drive shafting, generators, pumps, oil cooler
blowers, and engines. High frequency vibrations come from gears meshing and fan, turbine and compressor
blade passage. The Aviation Vibration Analysis (AVA) system allows you to collect spectrums at any appropriate
location by mounting an accelerometer on the airframe and utilizing the PROBES flight plan or the FFT (Fast
Fourier Transform) Aircraft Type. The PROBES flight plan allows vibration data to be taken on accelerometers
14 for one flight plan, and the range is from 030,000 RPM (0500 Hz). This range is usually sufficient to trouble
shoot most of the vibrations problems on the AH64. The FFT Aircraft Type has many different ranges, but it only
allows measurements to be taken on accelerometer number one. The only reason that the FFT Aircraft Type
needs to be utilized is if you know a source that you are looking for is above 30,000 RPM (500 Hz). This data can
be used for troubleshooting High Freq vibration problems, however you are pretty much on your own in
determining what is good and what is bad more on that latter.
The spectrum used in the PROBES or FFT flight plan is an asynchronous spectrum. This spectrum provides no
phase information as sampling starts at an arbitrary time and is not keyed to anything like a tack signal. The
spectrum displayed is an average of 16 spectra taken consecutively after you press measure and shows you the
vibration amplitudes induced at your measuring point by the forces from each rotating part.
MidFreq Vibrations (Drive Train induced vibration)
So as not to confuse most vibrations above 60 to 80 Hz will be called HiFreq vibration by a pilot. When a
HiFreq vibration is felt, maintenance action should be taken. The drive train has numerous rotating parts that
produce vibration at many different frequencies, locating the bad part is not an easy task.
Here are some things that might help. The table at the end of this section contains the frequencies of most, not all,
of the rotating parts of the AH64. Once per revolution (rotational speed of the component) vibrations are
associated with balance. Indexing a shaft at its mounting flange will change its balance. Two per rev (twice the
rotational speed) vibrations are associated with the alignment of shafts. An increase, in several harmonics of a
shaft (say 1R, 2R, 3R, and 4R) at the same time is indicative of bearing wear. A number of maintenance
personnel are troubleshooting HiFreq problems by taking data at identical locations on a good aircraft and the
HiFreq aircraft at the same time and comparing the differences. If there is a problem, comparing these two
displays should show which component is the cause.
Following are a few comments on vibration management based on spectrumbased monitoring. This method
simply identifies the amplitudes of vibration at frequencies associated with any rotating component (shaft rotation
speed and multiples thereof, gear mesh frequency, bearing ball pass frequency). This technology is widely used in
the industrial world for machinery monitoring and there are many vendors of both the hardware and software
required for implementation. On helicopters, it is good for monitoring shafting imbalance and misalignment,
bearing wear, and gross defects that a pilot would report as a HiFreq vibration (which can ground the aircraft
until removed). Profitable implementation depends on proper selection of monitored limits. When a limit is
exceeded, a maintenance action is required (replace, balance, align, or lubricate). Limits set too low affect
maintenance cost adversely. Limits set too high allow failure which may produce auxiliary damage and, perhaps,
loss of an aircraft. Spectrumbased monitoring has been touted by many as a valid tool for transmission health
monitoring. It is not. It can only detect a small percentage of impending failures and has the potential of producing
a large number of false alarms.
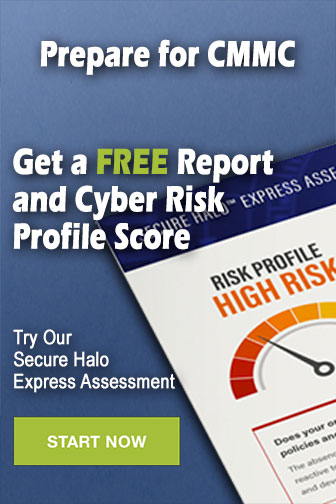