TM 1-1520-238-T-4
614
SECTION II.
THEORY OF OPERATION
67.
SYSTEM DESCRIPTION
67
a. The Drive System.
The drive system (fig. 69) transmits engine drive power from the engines to the
main rotor and tail rotor assemblies, it also transmits APU drive power to the main transmission accessory section
when the engines are not running.
(1) Engines 1 and 2 transfer drive power from each engine through an engine NGB assembly and an input
drive shaft to the main transmission assembly. The main transmission changes the angle and reduces the speed
of the drive input and transmits drive power to the main and tail rotor assemblies. The drive output is transferred
directly from the main transmission assembly to the main rotor head assembly through the main rotor drive shaft.
The drive output from the main transmission assembly is transferred to the tail rotor assembly through three drive
shafts to the IGB assembly. The IGB changes the angle, reduces the speed, and applies drive power through a
drive shaft to the TGB assembly. The TGB again changes the angle, reduces the speed, and transmits drive
power directly to the tail rotor head assembly.
(2) When the engines are not running the APU transmits input power to the accessory gear box through
the APU drive shaft 7 to drive the accessory drive section of the main transmission assembly. The accessory drive
section can also be driven by one or both engines. The accessory drive section provides electrical power
generation, pneumatic power, and hydraulic power.
(3) The drive system is designed to provide 30 minutes of operation with loss of lubricant. The shafts are
designed to prevent catastrophic failure if struck by a bullet. Specially designed antiflail assemblies prevent drive
shaft whip if a coupling were to fail.
(4) The engine NGBs are equipped with cooling fans that draw air across the engine NGB cooling fins
which directs the air down the drive shaft fairing into the transmission bay area. The IGB is fitted with a fan that
draws cooling air over the TGB and IGB assemblies and then vents the warm air overboard.
b. Purpose.
The drive system converts power from engine 1 and 2 to useful torque at the main rotor and
tail rotor assemblies by reducing the high rpm of the engines into usable power. The drive system also supplies
drive power to the electrical power generators and hydraulic system pumps.
c. System Operation.
(1) Tail Rotor Drive Shafts.
The tail rotor drive shafts provide a means for the main transmission to
drive the tail rotor. Drive shaft 3 transmits power from the main transmission to drive shaft 4. Drive shaft 4
transmits power from drive shaft 3 to drive shaft 5. Two bearing hangar assemblies support the drive shaft,
allowing it to turn. Damper assemblies permit the drive shaft to rotate through critical speeds while damping
natural frequencies. Drive shaft 5 transmits power from drive shaft 4 to the IGB assembly.
(a) The bearing hanger assemblies connect, support, and align drive shafts 3, 4, and 5. The forward
bearing hanger assembly provides positive center alignment with flange bearings that oscillate when subjected to
moving torque loads. Internal bearing clearance allows for a slight misalignment. The aft bearing hanger assembly
provides positive center alignment and allows it to swing fore and aft for axial alignment.
(b) The input clutch assemblies are freewheeling sprag type assemblies that provide drive and
disengaging capabilities for the main transmission. During emergencies, the main transmission disengages the
inoperative engine through the input overrunning clutch for single engine operation, or both engines can be
disengaged for authorization. A twohour overrunning is permissible without damage to the input clutches.
Complete loss of lubrication does not prevent full overrunning for a minimum of 30 minutes of emergency
operation. Increased backlash is provided in the bevel gears to accommodate for high thermal expansion which
occurs during emergency operations after the complete loss of lubricating oil.
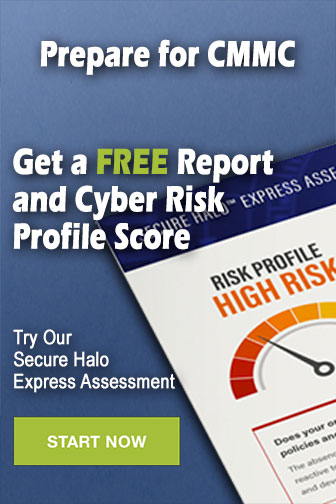