TM 1-1520-238-T-4
615
67.
SYSTEM DESCRIPTION (cont)
67
(2) Accessory Drive Section.
The accessory drive section can be driven by one or both engines
through the input drive shafts. When the engines are not operating, the APU drives the accessory drive section
through drive shaft 7. The APU drives the accessory gear train during ground operations when the main
transmission is operating at 95% NR or stopped. The accessory drive section powers two generators, two
hydraulic pumps, a SDC, and the accessory drive lubrication pumps.
(3) IGB Assembly.
The IGB assembly transmits power from the main transmission to the TGB assembly
while changing the drive angle. The IGB assembly reduces an input rpm of 4815 to an output rpm of 3636. The
housing supports the IGB internal gears, bearings, and drive shaft and provides mounting points for the IGB
assembly. Grease packed in the housing and static support provides cooling and lubrication during normal
operations, after a rotating gear seal failure, or after a ballistic impact. A breather vent prevents the IGB assembly
from being overpressurized. The assembly includes four temperature sensors (thermistors), accelerometer, and
fan assembly.
(a) Four temperature sensors monitor IGB bearing temperatures. Each sensor is a coilactivated
temperature sensing switch, springloaded to maintain contact with the bearing. When bearing temperatures
exceed operating limits of 274 to 294 F (134 to 146 C), the temperature sensors close, lighting the pilot and
CPG TEMP INT indicators.
(b) An accelerometer monitors vibrations inside the IGB assembly. Excessive vibration causes the
accelerometer to light the pilot and CPG caution/warning panel VIB GRBX indicators.
(c) Cooling air is provided through the ram air inlet port on the leading edge of the vertical stabilizer. A
cooling fan draws air through the fairing and down the stabilizer. The cooling air passes over the IGB housing.
The diffuser housing directs the air overboard through vent ports in the lower stabilizer fairing.
(d) Drive shaft 6 transmits power from the IGB to the TGB assemblies to drive the tail rotor head.
Couplings attach the drive shaft to the IGB and TGB assemblies and provide flexibility.
(4) TGB Assembly.
The TGB transmits power from the IGB assembly to the tail rotor head by reducing
the speed, increasing the torque, and changing the drive angle.
(a) The gear train in the TGB assembly changes the drive angle 90 and increases torque to the tail
rotor. The TGB assembly reduces an input rpm of 3636 from drive shaft 6 to an output rpm of 1403 to the tail
rotor. The gear train is packed with grease for lubrication and to aid in cooling.
(b) The static support transmits all drive loads to the tail rotor head through the center of the static
support. The static support transmits all tail rotor head flight loads to the housing. A quill shaft transfers power
from the gear train to the output shaft assembly. The output shaft assembly has a coupling for positive
engagement and provides for positive alignment of the tail rotor.
(c) Four temperature sensors (thermistors) monitor TGB bearing temperatures. Each sensor is a
coilactivated temperature sensing switch, springloaded to maintain positive contact with the bearing. When
bearing temperatures exceed operating limits of 274 to 294 F(134 to 146 C), the temperature sensors close,
lighting the pilot and CPG caution/warning panels TEMP TR indicators. A breather vent prevents TGB from being
overpressurized.
(d) The accelerometer monitors vibrations inside the TGB assembly. Excessive vibration causes the
accelerometer to light the pilot and CPG caution/warning panels VIB GRBX indicators.
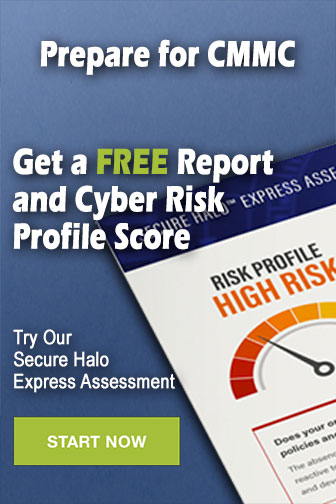