TM 1-1520-238-T-4
618
67.
SYSTEM DESCRIPTION (cont)
67
(6) Main Transmission Assembly.
The main transmission assembly provides primary drive for the main
and tail rotor drive shafts. The engine NGBs input 9841 rpm to the main transmission, which outputs 289 rpm to
the main rotor and 4815 rpm to the tail rotor drive shaft while increasing torque.
(a) The primary gear train reduces input speed from the NGBs and changes the drive angles of the
primary and accessory drives. The power takeoff clutches, two sprag clutch assemblies and a roller bearing, sets
freewheel without turning the primary gear train or tail rotor drive shaft when the main transmission assembly
operates at 100% NR. The primary gear train drives the magnetic pickup, two generators, two hydraulic pumps, a
shaft driven compressor, accessory oil pump, rotor brake disc, main rotor drive shaft and the tail rotor drive shaft.
A magnetic pickup in the accessory section signals main rotor rpm readout on the pilot and CPG ENGRTR
RPM% indicators. The magnetic pickup creates electrical impulses from the primary gear train motion. Two ac
generators provide ac electrical power for the helicopter. They also provide protection for the main transmission oil
sumps from ballistic impact. The primary and utility hydraulic pumps are constantpressure variable delivery,
piston type pumps that incorporate a shear shaft. The shaft driven compressor provides pressurized air for the
pressurized air system (PAS). The shaft driven compressor draws ambient air through the particle separator and
compresses it to 35 psi and operates automatically while the main transmission is operating or while being driven
by the APU. The shaft driven compressor is driven by the left generator spur gear. The rotor brake disc retards or
prevents main rotor drive shaft rotation. A steel disc is splined to the rotor gear shaft. Grip assemblies on each
side of the disc trap it when pressure is applied. The grip assembly incorporates selfreturn and selfadjusting
features. The RTR BK indicator on the pilot caution/warning panel lights when the brake is applied.
(b) The lubrication system (fig. 611) consists of the main transmission lubrication system and the
accessory lubrication system. Each system contains oilsaturated felt wicking devices inside beveled gears and
around helical gears. Lubrication is provide for a minimum of 30 minutes during emergency operations. Bearings
using silverplated steel races provide lubrication during the start period and aid with emergency lubrication.
(c) The main transmission lubrication system includes the primary oil system with two oil sumps, two oil
pumps, a gallery, two check valves, two pressure relief valves, two floater diverter valves, an oil filter assembly,
two chip detector/temperature switches, two oil pressure switches, two oil temperature transducers, and two
radialtype heat exchangers (mounted on the engine deck firewalls). Ten oil system jets are installed externally on
the main transmission housing to spray filtered oil directly on the components requiring lubrication.
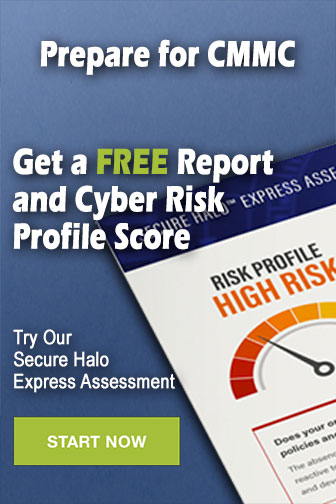