TM 1-1520-238-T-7
Change 5
1041
107.
SYSTEM DESCRIPTION (cont)
107
(b) During fuel transfer electrical operation (fig. 1016), 28 VDC is supplied to the pilots TRANS switch
or the CPGs ORIDE switch on the respective FUEL panel by the FUEL TRANS circuit breaker (CB56). When the
CPG selects the CPG ORIDE switch position on the CPG FUEL panel, the CPG TRANS switch is enabled and
the pilots TRANS switch is disabled. When the CPG ORIDE switch is in PLT position, the pilots TRANS switch is
enabled and the CPGs TRANS switch is disabled.
(c) When the pilots TRANS switch is enabled and set to TO FWD, 28 VDC is applied through pins 5
and 6 of the pilot TRANS switch to pin 3 of the fuel transfer valve and CR19. When the CPGs TRANS switch is
enabled and set to TO FWD, 28 VDC is applied through pins 5 and 6 of the CPGs TRANS switch to pin 3 of the
fuel transfer valve and CR19. (ADA) Current through CR19 is drawn from the instrument panel transfer fuel
indicators through the multi-channel dimming controller, causing the FUEL XFR/XFER indicators to light. (ADA) If
fuel does not transfer with the TRANS switch set to TO FWD, the caution/warning panel indicators FUEL XFR
(pilot) and FUEL XFER (CPG) light to indicate a failure. (ADB) Current through CR19 energizes relay K59
allowing the green FUEL XFR indicators to light if fuel transfers and the amber FUEL XFR indicators to light if
fuel does not transfer. Voltage at pin 3 is applied to the forward direction winding to unlock the brake and drive the
valve to port PAS air in the direction to transfer fuel from the aft fuel cell to the forward fuel cell. As the valve
leaves center position, switch S4 closes. When the valve reaches the full forward position, switch S1 opens,
removing power from the forward winding of the motor and locking the brake. After fuel has been transferred, the
TRANS switch is placed in the OFF position. This applies 28 VDC from pins 2 and 3 of the TRANS switches to pin
2 of the fuel transfer air valve. Voltage applied through the aft motor winding drives the valve in the aft direction.
Switch S1 closes as soon as the valve leaves the full position. When the valve reaches the center position, switch
S4 opens, removing power from the motor and locking the brake.
(d) When the pilots TRANS switch is enabled and set to TO AFT, 28 VDC is applied through pins 2 and
1 of the pilots TRANS switch to pin 1 of the fuel transfer valve and CR18. When the CPGs TRANS switch is
enabled and set to TO AFT, 28 VDC is applied through pins 2 and 1 of the CPGs TRANS switch to pin 3 of the
fuel transfer valve and CR18. (ADA) Current through CR18 is drawn from the instrument panel transfer fuel
indicators through the multi-channel dimming controller, causing the FUEL XFR/XFER indicators to light. (ADA) If
fuel does not transfer with the TRANS switch set to TO AFT, the caution/warning panel indicators FUEL XFR
(pilot) and FUEL XFER (CPG) light to indicate a failure. (ADB) Current through CR18 energizes relay K59
allowing the green FUEL XFR indicators to light if fuel transfers and the amber FUEL XFR indicators to light if
fuel does not transfer. Voltage at pin 1 is applied to the aft direction winding to unlock the brake and drive the
valve to port PAS air in the direction to transfer fuel from the forward fuel cell to the aft fuel cell. As the valve
leaves center position, switch S3 closes. When the valve reaches the full forward position, switch S2 opens,
removing power from the aft winding of the motor and locking the brake. After fuel has been transferred, the
TRANS switch is placed in the OFF position. This applies 28 VDC from pins 2 and 3 of the TRANS switches to pin
2 of the fuel transfer air valve. Voltage applied through the forward motor winding drives the valve in the forward
direction. Switch S2 closes as soon as the valve leaves the full position. When the valve reaches the center
position, switch S3 opens, removing power from the motor and locking brake.
(e) The fuel quantity transmitters (fig 1017) electronically measure the quantity of fuel in the forward
and aft fuel cells. The forward fuel cell contains two fuel quantity transmitters and the aft fuel cell contains one fuel
quantity transmitter. The aft fuel transmitter in each fuel cell contains a low level sensor. The low level outputs are
sent to the SDC. The fuel system is a capacitive sensing system which sends fuel cell data to the FSC.
(f) The SDC (fig. 1018) receives 28 VDC during normal operation and 24 VDC during refueling. The
input voltage is reduced for operation of the instrument system. Power is routed through an internal fuse panel to
two power supplies. The power supplies lower the 28 VDC to signal processing voltages. Operating power is also
routed to the FSC and engine torque sensors. The fuse panel provides instrument overload protection. The
forward and aft fuel cells send low fuel warning signals. The SDC outputs the signals to light the pilot and CPG
caution/warning panels FUEL LOW FWD and FUEL LOW AFT indicators.
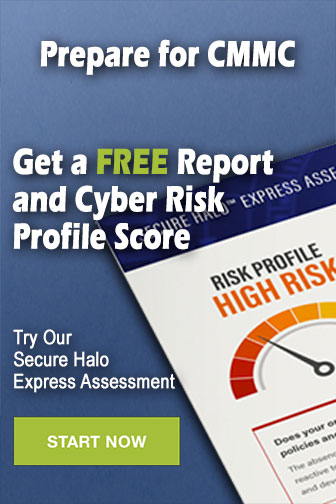