TM 1-1520-238-10
2-22
Section III.
ENGINES AND RELATED SYSTEMS
2.21 ENGINES.
The AH-64A helicopter can be equipped with either two
T700-GE-701
engines or two T700-GE-701C
engines. The engines are mounted horizontally and
housed in engine nacelles one on each side of the fuse-
lage aft of the main transmission above the wing. The en-
gines (fig 2-16) are a front-drive turboshaft engine of mod-
ular construction. The engines are divided into four
modules: cold section, hot section, power turbine section,
and accessory section.
2.21.1 Cold Section Module.
The cold section module
(fig 2-16) includes the main frame, diffuser and mid frame
assembly, the inlet particle separator, the compressor, the
output shaft assembly, and associated components. The
compressor has five axial stages and one centrifugal
stage. There are variable inlet guide vanes and variable
stage-1 and stage-2 stator vanes. Components mounted
on the cold section module are: the digital electronic con-
trol unit (DECU)
, the electrical control unit (ECU)
, anti-icing and start bleed valve, history recorder/his-
tory counter, ignition system, and electrical cables as well
as the accessory section module.
2.21.2 Hot Section Module.
The hot section module
(fig 2-16) consists of three subassemblies: the gas gen-
erator turbine, the stage one nozzle assembly, and the an-
nular combustion liner.
2.21.3 Power Turbine Section Module.
The power
turbine module (fig 2-16) includes a two stage power tur-
bine and exhaust frame. Mounted on the power turbine
module is the thermocouple harness, the torque and over-
speed sensor, and the Np sensor.
2.21.4 Accessory Section Module.
The accessory
section module (fig 2-16) includes the top mounted acces-
sory gearbox and the following components: a hydrome-
chanical unit (HMU), a fuel boost pump, oil filter, oil cooler,
alternator, oil lube and scavenge pump, particle separator
blower, fuel filter assembly, chip detector, oil/filter bypass
sensors, oil/fuel pressure sensor, overspeed and drain
valve (ODV), and an air turbine starter.
2.22 ENGINE COOLING.
Each engine is cooled by air routed through the engine
nacelle. Airflow is provided by eductor pumping action of
the infrared suppressor. Fixed louvers on the top and bot-
tom of the aft portion of each nacelle and moveable doors
in the bottom center forward portion of each nacelle accel-
erate convective engine cooling after shutdown. The
moveable door is shut by engine bleed-air pressure dur-
ing engine operation and is spring-loaded to open during
engine shutdown.
2.23 ENGINE AIR INDUCTION.
The engines receive air through a bellmouth shaped na-
celle inlet at the front of the engine. Air flows around the
nose gearbox fairing before entering the engine nacelle
inlet. From the inlet, air continues through canted vanes in
the swirl frame where swirling action separates sand,
dust, and other particles. Separated particles accumulate
by centrifugal force in a scroll case. The particles are
ejected overboard by a blower which forces them through
a secondary nozzle of the infrared suppression device.
Clean air, meanwhile, has passed through a deswirl vane
which straightens the airflow and channels it into the com-
pressor inlet.
2.24 INFRARED (IR) SUPPRESSION SYSTEM.
The IR suppression system consists of two assemblies:
the primary nozzle and three secondary nozzles. The pri-
mary nozzle is mounted to the engine exhaust frame and
directs exhaust gases into the secondary nozzle. The
three secondary nozzles are attached and sealed to the
engine nacelle with an adapter. During engine operation,
exhaust gases are cooled by air drawn through the trans-
mission area by a low pressure area created by the educ-
tion action of the primary nozzle. The angles of the prima-
ry and three secondary nozzles prevents a direct view of
the hot internal engine components. This also creates a
low pressure area which causes an eduction action by
drawing cooling air through the system. The cool air is
mixed with the hot air in the three secondary nozzles
which results in cooling the exhaust gases.
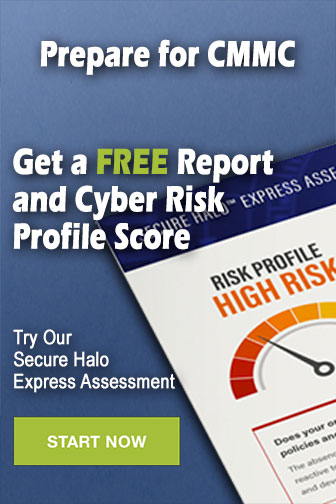