TM 1-1520-238-10
2-26
Change 9
NOTE
The ECU
and DECU
are not inter-
changeable between -701 and -701C en-
gines.
2.26.5 Electrical Control Unit (ECU)
.
The ECU
(fig 2-16) controls the engine and transmits operational in-
formation to the crew stations. It is a solid-state device
mounted below the engine compressor casing. Powered
by the engine alternator, the ECU receives inputs from the
thermocouple harness, Np sensor, torque and overspeed
sensor, opposite engine torque for load sharing, NG signal
from the alternator, Np reference signal from the turbine
speed control unit, and a feedback signal from the HMU
for system stabilization. The torque-sharing system in-
creases power on the lower-output engine to match it with
the higher output engine. The ECU also receives opposite
engine torque inputs to enable contingency power. When
this input signal is 51% torque or below, contingency pow-
er is automatically enabled. However, contingency power
is not applied until the flight crew pulls in collective above
867 C TGT. The ECU automatically allows the normally
operating engine to increase its TGT limit, thereby in-
creasing its torque output. The overspeed protection sys-
tem senses a separate Np signal independently of the
governing channel. ECU also provides signals to the Np
indicator, TORQUE indicator, and history recorder. In case
of the ECU malfunction, system operation may be overrid-
den by momentarily advancing the engine PWR lever to
LOCKOUT and then retarding the lever past the FLY posi-
tion to manually control engine power. This locks out the
ECU from all control/limiting functions except Np over-
speed protection, which remains operational. To remove
the ECU from lockout operation, the engine PWR lever
must be moved to IDLE, then back to FLY.
a. Engine TGT Limiter Function
.
The ECU in-
corporates a steady state dual and single engine TGT lim-
iting function which restricts fuel flow within the HMU to
prevent an engine overtemperature. The limiting function
has an inherent 4 C variance. The resistance in the cab-
ling and circuitry between the ECU and TGT gauge is
enough to produce a 5 C variance factor. Applying the
sum of these two factors, the dual engine limiter setting is
allowed a value of 860 9 C (851 869 C) and the
single engine (contingency power) limiter setting is al-
lowed a value of 917 9 C (908 926 C). The TGT lim-
iter setting for a particular engine can change within these
ranges over a period of time.
2.26.6 Digital Electronic Control Unit (DECU)
.
The DECU (fig 2-16) is mounted in the same loca-
tion as the ECU. The DECU can be overridden like the
ECU by momentarily advancing the engine PWR lever to
LOCKOUT. The DECU, which incorporates improved
technology, performs the same functions as the ECU ex-
cept for the following functional and control improve-
ments.
The DECU can be fully powered by either the engine alter-
nator or by 400 Hz, 115 vac aircraft power. It incorporates
logic which will eliminate torque spike signals during en-
gine start-up and shutdown. The DECU control logic con-
tains a Maximum Torque Rate Attenuator (MTRA) feature
designed to reduce the risk of exceeding the dual engine
torque limit during uncompensated maneuvers. These are
any maneuvers where pedal or cyclic inputs are made but
no collective control inputs occur. For example, large tran-
sient engine torque increases can occur during left pedal
and left lateral cyclic inputs when performing maneuvers
such as rapid hovering turns or forward flight roll rever-
sals. The MTRA is designed to reduce fuel flow and limit
rate of torque increase to approximately 12% per second
when at transient engine torque during an uncompen-
sated maneuver. However, any collective control increase
during the maneuver can override the MTRA and normal
maximum engine torque rate increase can be achieved.
The MTRA feature is not active in the DECU logic under
single engine conditions. The DECU contains an automat-
ic hot start preventer (HSP). The DECU also provides sig-
nal validation for selected input signals within the electri-
cal control system. Signals are continuously validated
when the engine is operating at flight idle and above. If a
failure has occurred on a selected input signal, the failed
component or related circuit will be identified by a pre-se-
lected fault code. Fault codes will be displayed on the en-
gine torque meter (fig 2-18), which defines fault codes in
terms of engine torque. Fault codes will be displayed start-
ing with the lowest code for four seconds on/two seconds
off, rotating through all codes and then repeating the
cycle. The fault codes will be displayed on the engine
torque meter only when all of the following conditions are
met:
NG less than 20%
Np less than 35%
Other engine shutdown
Aircraft 400 Hz power available
The fault codes can be suppressed by pressing either
OVSP TEST switch. The fault codes can be recalled by
again pressing either OVSP TEST switch. Once a failure
has been identified, the fault code will remain available for
diagnostic indication until starter dropout on the next en-
gine start.
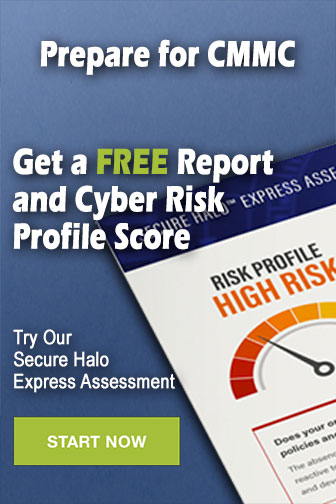