TM 1-1520-238-10
2-50
Change 4
Section VI.
HYDRAULIC AND PRESSURIZED AIR SYSTEMS
2.38 HYDRAULIC SYSTEMS.
Two independent hydraulic systems are installed so that
failure of one system will not affect operation of the other.
They are designated as the primary and utility hydraulic
systems. They are similar but not identical; they have sep-
arate, as well as shared functions.
2.38.1 Primary Hydraulic System.
The primary hy-
draulic system (fig 2-29) provides hydraulic power to the
primary side of the lateral cyclic, longitudinal cyclic, collec-
tive, and directional servoactuators. Only the primary
sides of these servoactuators (discussed in more detail in
Section V) have electrohydraulic valves that allow the
DASE and BUCS to affect the flight controls. Consequent-
ly, failure of the primary hydraulic system will result in the
loss of DASE and BUCS. The primary hydraulic equip-
ment includes the hydraulic pump, manifold, and servoac-
tuators. The heat exchanger may still be installed in the
primary system on some helicopters. The heat exchanger
is obsolete and is being removed through attrition.
a. Servoactuators.
The servoactuators (fig 2-29)
can be commanded mechanically or electrically. Each ac-
tuator contains two hydraulic pistons on a common piston
rod. One piston is driven by the primary hydraulic system,
the other by the utility hydraulic system. The hydraulic pro-
visions in the actuator are completely independent of
each other; there is no exchange of fluid between sys-
tems.
Each actuator is controlled by a common manual tan-
dem servo valve which ports hydraulic pressure to each of
the pistons. The servo valve spool is positioned by the as-
sociated mechanical control system to provide full author-
ity control. Each actuator is also electrically controlled
through the electrohydraulic valve sleeve to provide SAS
or BUCS control. Each actuator is equipped with a hy-
draulically powered plunger which locks the manual servo
valve spool at mid position when the DASEC powers the
BUCS solenoid valve for BUCS engagement. Each actua-
tor is also equipped with a DASEC controlled SAS sole-
noid valve that ports primary hydraulic pressure to the ser-
vo valve and the BUCS solenoid. Position transducer
LVDTs measure the position of the servo valve sleeve
and the actuator position. Each actuator incorporates a
shear pin in the feedback linkage to decouple the actuator
motion from a jammed mechanical control and prevent
damage to the bellcrank attachments.
b. Primary Pump.
The primary hydraulic pump is
mounted on the accessory drive case of the main trans-
mission (left side). The pump is of constant-pressure vari-
able-displacement design driven by the transmission ac-
cessory gear train.
c. Primary Manifold.
The primary manifold is
installed on the left forward quadrant of the transmission
deck. Its function is to store, filter, supply, and regulate the
flow of hydraulic fluid. The manifold reservoir is pressur-
ized on the return side by PAS air acting on the manifold
reservoir piston. This prevents pump inlet cavitation. Ser-
vicing crews introduce fluid to the reservoir through
ground support equipment (GSE) connections or the hand
pump. Low pressure fluid entering the fill port is filtered by
a 45 micron screen filter (before MWO 1-1520-238-50-52)
or a 5 micron cartridge filter (after MWO
1-1520-238-50-52). The primary hydraulic system fluid
capacity is six pints. The reservoir stores about one pint.
Section XV contains specifications, capacities, and proce-
dures for oil system servicing. Other provisions within the
primary manifold are described below:
(1) Air-Bleed Valve.
Used to deplete the pres-
surized air on the manifold for system repair or service.
(2) High-Pressure and Low-pressure Relief
Valves.
Regulates fluid pressure from the pump and the
return to the manifold.
(3) Reservoir Low-Level Indication Switch.
Switch is activated by the manifold reservoir piston. This
illuminates an OIL LOW PRI HYD segment light on the pi-
lot caution/warning panel to indicate minimum operating
level.
(4) Fluid Level Indicator.
Located in the man-
ifold reservoir housing allows visual inspection of the res-
ervoir oil level.
(5) Filters.
Filters on both manifold pressure
and return sides have mechanical impending bypass indi-
cators for visual inspection. These indicators operate on
differential pressure. Both impending bypass indicators il-
luminate the OIL BYP PRI HYD segment on the pilot cau-
tion/warning panel. Only the return filter has bypass provi-
sions.
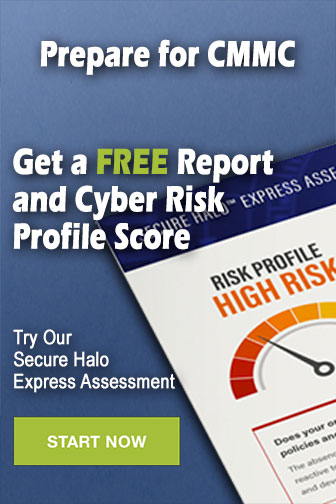