TM 1-1520-238-23
Change 11
1-402.19
1.137.
SPECIAL INSPECTION CHECKLIST continued
Helicopter Serial No.:
Date:
Area
No.
Special
Inspection
No.
REQUIREMENT
EVERY
Item
Status
4
50A
(cont)
b. No later than next 10 hour/14 day inspection, perform torque check of
three nuts, securing the T/R fork to the T/R gearbox output shaft (item 5,
paragraph 5.61.3.A). Using a torque wrench set to 600 inch-pounds,
attempt turn each nut in a clockwise direction. Any rotation of the nut
before 600 inch-pounds in unacceptable.
c. If nut rotation does not occur before 600 inch-pounds, verify proper
indexing of tail rotor fork using paragraphs 50A.d.(1) through 50A.a.d.(12)
no later than next 250 hour phase inspection.
d. If rotation of any of the nuts occurs before 600 inch-pounds, verify proper
indexing of tail rotor fork using paragraphs 50A.d.(1) through 50A.d.(12)
prior to the next flight.
NOTE
Task 5.6.1 refers to a single stud marked with an x on the end. An x
on the stud may be unreliable and should be ignored. Positive verifica-
tion of alignment shall be accomplished prior to each T/R head installa-
tion.
(1) Locate the number 1 hole in the T/R fork. The number 1 hole is the
hole adjacent to the teeter stop arm. for clarification, refer to item 3 in
paragraph 5.61.3 (a). Apply torque strip paint around this hole (not
the stud).
NOTE
The following inspections are performed on the aircraft with T/R blades
installed.
(2) Remove the three nuts securing the fork to the T/R output shaft. If
any threads on the studs are crossed, stripped, or flattened, or if
obvious necking of the threads is evident on the stud, replace the bad
stud in accordance with paragraph 50A.c
CAUTION
Do not allow the T/R head assembly to rest on the studs while the T/R
assembly is slid out. Excessive bending loads may damage the studs.
(3) Using two persons or an overhead hoist/crane to support the hub
(while a third person performs the inspection below) slide the T/R
head assembly out approximately 2-1/2 inches. (Do not completely
remove the fork from the studs).
(4) Rotate the output drive on the clutch while observing the needle
bearing. If the shaft does not rotate smoothly or the shaft/needle
bearing does not remain centered, replace the clutch.
GO TO NEXT PAGE
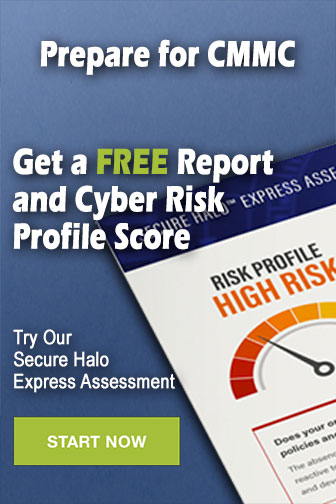