TM 1-1520-238-23
7-235
7.56.
UTILITY HYDRAULIC SYSTEM INSPECTION continued
c. Check for chafed, cracked, dented, nicked, and scored tubes.
(1) Replace tube assembly if tube is deformed or if nuts and unions are damaged (para 7.113).
(2) Replace tube assembly if tube is dented more than 20 percent of tube diameter (para 7.113).
(3) Replace tube assembly if nicked or chafed more than 10 percent of tube wall thickness (para 7.113).
(4) Install screws until mating rubber cushions just make contact when reinstalling rubber cushioned tubing
clamp blocks.
d. Check for chafed, deteriorated, cut, frayed, and cracked hoses. Replace damaged or worn hoses.
e. Check for loose, broken, and cracked clamps. Replace damaged clamps.
f. Check utility hydraulic manifold reservoir fluid level. Service as required (para 1.34).
g. Check and replace contaminated strainers (para 7.69).
h. Check nitrogen gas charge in pneumatic accumulator as indicated on utility ground service panel.
Service as required (para 1.36).
i. Check for leaks. No external leakage allowed except at servocylinder rod ends and at the cylinder mating
flange of directional and main rotor servocylinders. Perform the following to determine if leakage is excessive:
(1) Slight wetting at seals or signs of fluid insufficient to form a drop is considered seepage or residual fluid and
is not external leakage.
(2) Wipe servocylinder clean of any fluid at rod end, weep hole, or mating flange.
(3) Operate flight controls through a minimum of 25 full-stroke cycles with hydraulic systems pressurized to
3000 psi (with ground power or APU operating).
(4) Leakage at the rod end or at the weep hole shall not exceed 1 drop in 25 cycles; leakage at the mating
flange shall not exceed 2 drops in 25 cycles.
NOTE
The double rod seal at the mating flange of the servocylinders is in a floating gland which moves
slightly when the servocylinder is cycled. This results in a pumping action which produces a breath-
ing of fluid at the mating flange. This breathing of fluid is not to be considered leakage.
(5) Utility hydraulic pump seal drain maximum seepage: 5 drops in 3 minutes.
(6) When external servocylinder leakage is observed on aircraft standing idle for any length of time, wipe
servocylinder and clean up any fluid spillage. Perform hydraulic systems maintenance operational check
(MOC) and inspect for dynamic seal leaks [reference steps i.(1) through i.(4)]. Static leakage is allowed
and is not cause for servocylinder removal.
GO TO NEXT PAGE
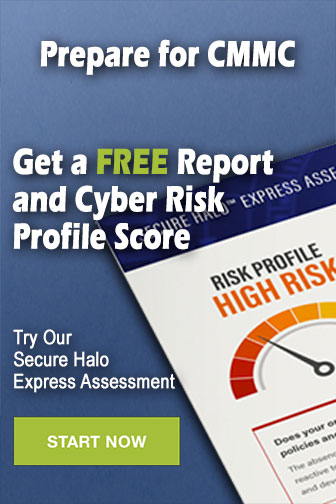