TM 1-1520-238-10
2-58
a. Rotor Brake (RTR BK) Switch.
The rotor brake
is controlled by the RTR BK switch on the pilot PWR lever
quadrant (fig 2-19). The switch has three positions: OFF,
BRAKE, and LOCK. When set at LOCK with full utility hy-
draulic system pressure, the brake prevents the gas tur-
bines from driving the power turbines when both engines
are at idle. When the rotor is stopped, the switch may be
set at LOCK which causes solenoid valves in the manifold
to deenergize and all available utility hydraulic system or
accumulator pressure to be applied to the brake. A system
of interlocks prevents the rotor brake from being locked
when the PWR levers are in any position except IDLE and
OFF. When the switch is set at BRAKE, solenoid valves in
the utility hydraulic manifold operate to actuate the brake.
With the switch at OFF, the only hydraulic pressure to the
brake is 30 psi from the pressurized air system which,
when operating, pressurizes the return side of the utility
hydraulic system.
b. Rotor
Brake
Solenoid
and
Pressure
Switch.
Rotor brake electrical solenoids and the pres-
sure switch receive 28 vdc from the emergency dc bus
through the RTR BRK circuit breaker on the pilot over-
head circuit breaker panel. If this circuit breaker is open,
or if helicopter emergency electrical power is lost for any
reason, the rotor brake, if previously set at LOCK, will re-
main locked as long as accumulator pressure is available.
2.40.4 Tail Rotor Drive Shafts.
There are four tail rotor
drive shaft sections. Three tail rotor drive shafts lead from
the transmission to the intermediate gearbox. Two are of
equal length. The last shaft is installed on the vertical sta-
bilizer between the intermediate and tail rotor gearboxes.
Hanger bearings support the longer shafts. They are cov-
ered by aerodynamic fairings which may be opened for
maintenance and inspection. The two equal-length shafts
incorporate friction dampers and antiflails. Flexible cou-
plings, attached to the shaft ends, are capable of accom-
modating shaft misalignments throughout the power
range.
CAUTION
Prolonged out of ground effect hovering
(20 30 min.) with outside air tempera-
tures above 75 F (24 C) may cause the
intermediate gearbox to overheat.
2.40.5 Intermediate Gearbox.
The intermediate gear-
box, at the base of the vertical stabilizer, reduces the rpm
and changes the angle of drive. A fan mounted on the
gearbox input shaft draws air from an inlet on the vertical
stabilizer. This air cools both the tail rotor gearbox and the
intermediate gearbox. Four thermistors monitor tempera-
ture and an accelerometer measures vibration limits. The
intermediate gearbox is a grease-lubricated sealed unit.
a. Intermediate Gearbox Caution Light Indica-
tors.
The four thermistors and the accelerometer pro-
vide crewmembers with temperature and vibration caution
lights. Both crew stations have TEMP INT and VIB GRBX
light segments.
CAUTION
Prolonged out of ground effect hovering
(20 30 min.) with outside air tempera-
tures above 75 F (24 C) may cause the
tail rotor gearbox to overheat.
2.40.6 Tail Rotor Gearbox.
The tail rotor gearbox,
mounted on the vertical stabilizer, reduces the output rpm
and changes the angle of drive. The tail rotor output shaft
passes through the gearbox static mast. All tail rotor loads
are transmitted to the static mast. The output shaft trans-
mits only torque to the tail rotor. Lubrication of this gear-
box is identical to that of the intermediate gearbox.
a. Tail Rotor Gearbox Caution Light Indica-
tors.
The four thermistors and the accelerometer func-
tion in the same way as for the intermediate gearbox. The
associated caution light on the pilot and CPG caution/
warning panels are labeled TEMP TR and VIB GRBX.
(Both the intermediate and tail rotor gearboxes activate
the VIB GRBX light segment).
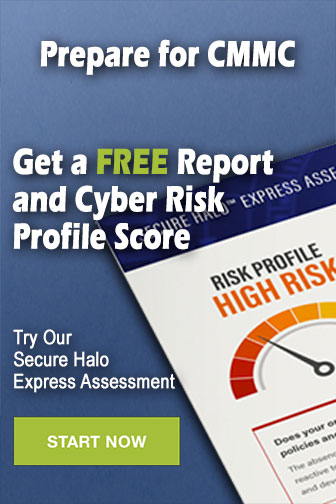