TM 1-1520-238-10
2-61
AIR DATA DC circuit breaker to the left wing pitot heater.
Both circuit breakers are on the pilot overhead circuit
breaker panel. The AIR DATA DC circuit breaker also pro-
vides 28 vdc to the ADS control relay. When energized,
this relay sends 115 vac from the No. 1 essential ac bus
through the AIR DATA AC circuit breaker to the air data
sensor for anti-icing. In addition, the CPG AUX panel
ADSS switch, when set to on, energizes the ADS control
relay to provide the air data sensor with 115 vac from the
No. 3 essential ac bus through the AIR DATA AC circuit
breaker.
2.43.3 PNVS and TADS Anti-Ice/De-Ice.
Three posi-
tion TADS/PNVS toggle switches on the pilot ANTI-ICE
panel and the CPG AUX/ANTI-ICE panel control the op-
eration of the TADS/PNVS window heaters. These
switches receive 28 vdc from the No. 1 essential dc bus
through the CANOPY ANTI-ICE CONTR circuit breaker.
Window heating is automatically controlled by a thermal
control sensor in the respective heater power return cir-
cuits.
a. In Flight TADS/PNVS Anti-Ice/De-Ice.
With the
helicopter in flight and the pilot or CPG TADS/PNVS
switch set to ON, the squat switch relay closes to provide
28 vdc from the pilot or CPG TADS/PNVS switch to the
MRTU. This causes the MRTU to send a signal to ener-
gize anti-ice relays in the TADS power supply and PNVS
electronic unit. The TADS and PNVS anti-ice relays then
provide the TADS and PNVS window heaters with 115 vac
from the No. 1 essential ac bus through the TADS AC on
the CPG circuit breaker panel and the PNVS AC circuit
breakers on the pilot overhead circuit breaker panel.
b. On Ground TADS/PNVS Anti-Ice/De-Ice.
When
the helicopter is on the ground, the squat switch opens re-
moving power from the TADS/PNVS switches and the
TADS and PNVS window heaters. When either TADS/
PNVS switch is set to GND, a signal is sent to the MRTU
which energizes the TADS/PNVS anti-ice relays. These
relays then provide the TADS and PNVS window heaters
with 115 vac from the No. 1 essential ac bus through the
TADS AC and PNVS AC circuit breakers.
2.43.4 Engine Inlet and Nose Gearbox Anti-Ice.
En-
gine bleed air is used to heat the engine air inlet, and heat-
er blankets are used to anti-ice the nose gearbox. Engine
anti-ice protection is controlled by a ENG INLET ON/OFF
toggle switch on the pilot ANTI-ICE panel. In the ON posi-
tion, ENG 1 and ENG 2 advisory lights located above the
switch will illuminate when the system is functioning prop-
erly. The engine anti-ice valves and engine gearbox heat-
er blanket controller receive 28 vdc from the No. 1 essen-
tial dc bus through the ENG ANTI-ICE circuit breaker on
the pilot overhead circuit breaker panel. The ENG INLET
switch in the OFF position energizes both engine anti-ice
valves to the closed position. In the ON position, the ENG
INLET switch deenergizes the anti-ice valves thus allow-
ing them to open and furnish hot air to the engine inlet for
anti-icing. It also energizes the engine gearbox heater
blanket controller. The energized controller allows 115 vac
to be supplied from the No. 1 essential ac bus through the
NOSE GRBX HTR circuit breaker on the pilot overhead
circuit breaker panel for the nose gearbox heater blan-
kets.
2.43.5 Rotor Blade De-Icing System.
The rotor blade
de-ice three-position ON, OFF, and TEST toggle switch,
located on the pilot ANTI-ICE panel receives 28 vdc from
the No. 3 essential dc bus through the BLADE DE-ICE
CONTR circuit breaker on the pilot overhead circuit break-
er panel. In the ON position, the switch will provide 28 vdc
power to the main rotor and-tail rotor de-icing controller
and turn on the controller. When the controller is turned
on, it collects data from the signal processor unit, ice de-
tector/rate sensor, and the outside air temperature sensor.
If icing conditions are present, the controller will energize
the blade de-ice control relay. The energized blade de-ice
control relay provides a ground to the blade de-ice contac-
tor control relay that receives 28 vdc from the No. 3 es-
sential dc bus through the BLADE DE-ICE circuit breaker.
With the blade de-ice contactor energized, 115 vac, 3
phase power is furnished from Gen 2 through the blade
de-ice contactor to the de-ice controller. (Gen 1 will only
furnish power when an overload is sensed on Gen 2, and
the contactor is caused to trip). The de-ice controller recti-
fies the 115 vac to 268 vdc ( 134 vdc) for the rotor blade
heaters. The main rotor blades receive 134 vdc through
slip rings at the main rotor distributor. The main rotor dis-
tributor provides a sequential delivery to the blade heater
elements. In the TEST position, the rotor blade de-ice
switch provides that the controller will complete one full
cycle of the blade anti-ice circuits. The tail rotor blades re-
ceive 134 vdc from the de-icing controller through tail
rotor slip rings. Power to the tail rotor blade elements and
main rotor blade elements is controlled by the de-icing
controller which times the amount of current allowed to the
blades for heating. The de-icing controller will detect faults
within the system. When a fault occurs, the controller
shuts off power to the blades and illuminates the BLADE
ANTI ICE FAIL segment on the pilot caution/warning pan-
el.
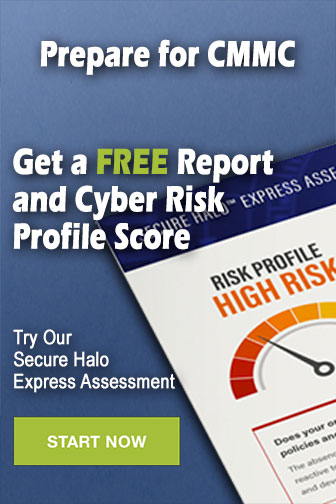