TM 1-1520-238-10
2-59
Section VIII. ROTORS
2.41 ROTOR SYSTEM.
The rotor system consists of a single, four-bladed, fully ar-
ticulated main rotor and a four-bladed tail rotor assembly
with two teetering rotor hubs.
2.41.1 Main Rotor.
The main rotor has four blades. The
head is a fully articulated system that allows the four
blades to flap, feather, lead, or lag independent of one
another. The head consists of a hub assembly, pitch hous-
ings, rotor dampers, and lead-lag links. Attached to the ro-
tor head are four easily removable blades. The main rotor
is controlled by the cyclic and collective sticks through a
swashplate mounted about the static mast.
a. Hub Assembly.
The main rotor hub is a steel and
aluminum assembly that supports the main rotor blades; it
is driven by the main rotor drive shaft. The hub rotates
about a static mast, which supports it. This arrangement
allows the static mast, rather than the main rotor drive
shaft, to assume all flight loads. The hub is splined to the
main rotor drive shaft by means of a drive plate adapter
that is bolted to the hub. The hub is secured to the static
mast by a large locknut secured by multiple bolts. The hub
houses two sets of tapered roller bearings that are
grease-lubricated and sealed. These bearings transfer
hub loads to the static mast. Mechanical droop stops limit
blade droop. When blade droop occurs, a striker plate on
the pitch housing contacts a roller. The roller presses a
plunger against a droop stop ring on the lower portion of
the hub.
b. Pitch Housing.
The pitch housing permits blade
pitch changes in response to flight control movements
transmitted through the swashplate. This is made pos-
sible within the four pitch housings by V-shaped stainless
steel strap assemblies that are able to twist and flap to
permit blade feathering and flapping. Cyclic and collective
stick inputs are transmitted to the pitch housing horns by
pitch links attached to the swashplate. Feather bearings
are installed inboard on the pitch housing to allow vertical
and horizontal loads to be transferred from the pitch hous-
ing to the hub. Centrifugal loads are transmitted by each
strap assembly to the hub.
c. Lead-Lag Links.
The lead-lag link for each blade
is connected to the outboard end of each pitch housing
and is secured in place by a pin and two bearings that al-
low the link to move horizontally. The pin goes through the
V-portion of each strap within the pitch housing.
d. Damper Assemblies.
Two damper assemblies
control the lead-lag movement of each main rotor blade.
Each damper attaches outboard to a link lug and inboard
to a trunnion at the pitch housing. The damper contains
elastomeric elements that distort to allow the blade to lead
or lag.
e. Main Rotor Blades.
Each main rotor blade is a
constant-chord asymmetrical airfoil. The outboard tip is
swept aft 20 and tapers to a thinner symmetrical section.
The blade has a 21-inch chord. Tip weights are installed
within the blade. Chord-wise, the leading-edge and for-
ward half of the blade is a four-cell structural box of stain-
less steel and fiberglass with a stainless steel spar. The
aft half of the blade has fiberglass skin with a nomex hon-
eycomb core and a bendable trailing edge strip to aid in
blade tracking. Each blade secured to its lead-lag link by
two blade attachment pins. These pins can be removed
without the use of tools and they pass vertically through
the lead-lag link and blade root fittings which are both
made of titanium. Five sets of stainless steel doublers are
located on the upper and lower surfaces of the blade at
the blade root. The blades may be folded by removing the
appropriate blade attachment pin (one for each blade)
and any two adjacent pitch link bolts and pivoting the
blade to the rear position using a hand-held blade support
device.
2.41.2 Tail Rotor.
The tail rotor is of semirigid, teetering
design. Two pairs of blades, each pair fastened to its own
delta hinged hub, provide antitorque action and directional
control. A titanium fork houses two elastomeric teetering
bearings and drives the rotating swashplate through an
attached scissors assembly. The tail rotor assembly is
splined to, and driven by, the tail rotor gearbox drive shaft
which passes through a static mast. Blade pitch changes
when directional control inputs cause the non-rotating
swashplate to act upon the rotating swashplate. One pitch
link for each blade, attached to the rotating swashplate
and pitch horn, causes blade movement about two pitch-
change bearings in the blade root. Centrifugal forces are
carried by stainless steel strap assemblies that attach out-
board to the blade root and inboard at the hub center. An
elastomeric bearing assembly positions the hub and strap
pack in the tail rotor fork. Each blade has one stainless
steel spar and two aluminum spars. Doublers and rivets
attach the blade to the blade root. Brackets on the root fit-
ting hold chord-wise balance weights. Spanwise balance
weights are installed at the tip of each blade in an alumi-
num tip cap.
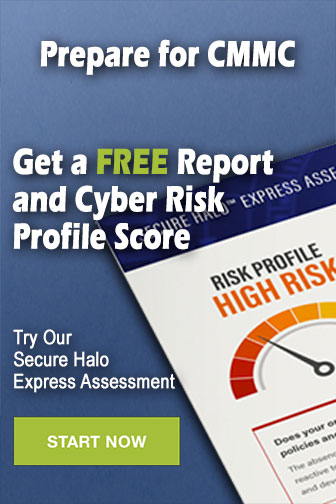