TM 1-1520-238-23
2-12
Change 4
2.1.
ACCESS PROVISIONS INSPECTION/REPAIR continued
NOTE
Steps (9), (10), and (11), refer to aircraft equipped with EMI provisions.
Damage orientations and categories contained in step (10), determine serviceability of the EMI
conductive coating. The EMI conductive coating protection is divided into three (I,II, and III) catego-
ries of importance.
(9) Check for damage, cuts, tears, and punctures in EMI gasket. Repair damage (para 2.27).
(10) Check for damage, cuts, scratches, cracking, or peeling in EMI conductive coating. Repair damage (para
2.34).
(11) Check for damage, cracking, or peeling in EMI tape. Repair damage (para 2.28).
NOTE
Category I areas should be repaired prior to flight operations in EMI environments of 200 volts/meter
or higher.
Category I areas include enclosures shielding critical equipment and wire harnesses. Shielding
effectiveness: 60-40 db.
(a) EMI conductive coating Category I areas. Category I conductive coating areas are the most critical and
should be in good condition (i.e. scratch free) with minimum defects.
1 Check mating surface of conductive coating to gasket or joining surface for contaminates and paint
over spray. Conductive coating surface can be cleaned by carefully using a soft cloth dampened
with isopropyl alcohol. Ensure conductive coating is not softened or damaged.
2 Scratched conductive coating around fasteners is allowable if gap is limited to one side of fastener
and not wider than 0.25 INCH.
NAME/
ACCESS NO.
ACCESS TO
PART NUMBER
NSN
CATEGORY
Door R90
Laser, PNVS, MUX, HF
Remote
7-311111223-46
I
Door L90
IHADSS and PNVS Boxes
and ICU
7-311111223-45
I
Fairing R60
Forward Avionics Bay Nose
7-311111223-606
I
Fairing L60
Forward Avionics Bay Nose
7-311111223-605
I
PNVS Shroud
Assembly
13080400039
5340-01309-1338
I
Door R295
Aft Electronics Equipment
7-311113690-50
I
END OF TASK
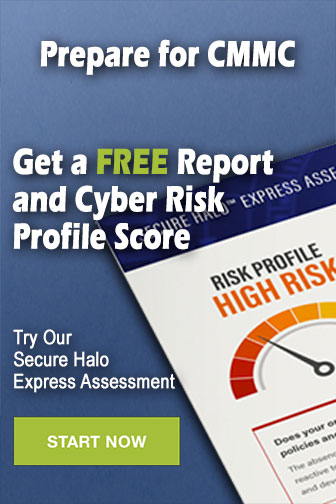