TM 1-1520-238-T-4
315
37.
SYSTEM DESCRIPTION (cont)
37
(b) Trailing Arm Assembly.
When the wheels contact the ground during landing, the trailing arms
pivot (rotate) down, transferring the vertical load inputs to the shock struts. As the weight of the fuselage is
supported by the MLG, the squat switch target on the left MLG moves out of proximity with the squat switch
(proximity switch). The proximity switch deenergizes a set of relays which in turn: (When the helicopter becomes
airborne, the shock struts extend causing the trailing arms to rotate up and move the squat switch target back into
proximity of the squat switch. This causes the relays to become energized and returns to its previous condition.)
Enables the wingmounted intercommunication system (ICS) receptacles.
Activates the generator underfrequency protection circuit.
Commands the pylon ejector racks to the ground stow position.
Enables the fault detection/location system (FD/LS) ground test.
Disables the laser, gun, rockets, and missiles.
Disables the yaw function of the digital automatic stabilization equipment (DASE).
Removes electrical power from the TADS/PNVS antiice circuit.
Erases the code in the TSEC/Kit1A if IFF mode 4 has been selected.
(c) Shock Strut Assembly.
The lower chamber of the cylinder and the lower piston are filled with
hydraulic fluid. The upper strut assembly is filled with dry nitrogen. During operation, the internal floating
diaphragm rides on top of this hydraulic fluid and compresses the nitrogen for a dampening effect of shocks
received to the fuselage. When the helicopter is in flight (or on jacks), nitrogen pressure forces the floating
diaphragm toward the lower end of the piston driving the piston to the extended position. The rate of extension is
controlled by an internal poppet valve and orifices at the lower end of the piston. Servicing of the strut is
accomplished through the hydraulic fill/bleed port, and a nitrogen fill/bleed port. Two vent ports at the lower
chamber, either side of the kneeling coupling, are used during servicing. Several markings are stenciled on the
strut to indicate location of valves, plugs, ports, and locking positions. A data plate gives shock strut inflation,
instructions, and servicing procedures. During takeoff, as the upper piston extends the controlled rate of fluid flow
prevents the MLG from dropping too fast. An elastomer spring assembly, installed internally in the top portion of
the upper cylinder, provides damping during extension. During landing, the weight of the helicopter causes the
shock struts to compress. The upper piston is forced toward the bottom of the cylinder. The poppet valve and
orifice, in the upper chamber valve assembly, controls the rate of fluid flow between the piston and cylinder as the
upper piston moves in and out. The floating diaphragm is forced upward by fluid pressure increasing the nitrogen
pressure against the upper side of the diaphragm. The compression of the nitrogen acts as a spring to cushion
the landing. A fuse collar mates with the machined flanges on the exterior surface of the lower piston. A quick
release pin is used to secure the fuse collar in the lock position. Three retaining pins (screws) prevent the fuse
collar from pulling away from the cylinder when the collar is disengaged from the internal flanges. The external
operating surface of the piston is chrome plated, with a red band around the upper portion of the lower piston
housing which provides visual indication of proper piston extension for fuse collar to flange engagement. The
lower end of the piston attaches to the trailing arm through a spherical selflubricating bearing installed in the
lower piston.
(d) Kneeling/Erecting.
The kneeling/erecting operation of the helicopter can be started by connecting
external hydraulic pressure to the kneeling couplings on both struts (TM 1-1520-238-23). When the fluid in the
cylinder is externally pressurized, the shear collars are unlocked. Fluid pressure is then slowly reduced to allow
the lower pistons to move into the lower cylinder chambers. This controlled method of lowering the helicopter
avoids damage to the aircraft. To raise the helicopter, external pressure is applied to the cylinders until the pistons
are fully extended. The shear collars are then locked.
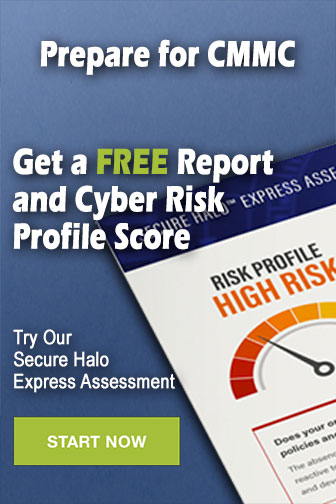