TM 1-1520-238-T-4
318
37.
SYSTEM DESCRIPTION (cont)
37
(e) Tail Wheel Lock Actuator System (fig. 315).
When the actuator is in the locked position,
fuselage reaction is minimized to rotor torque and crosswind effects. The lock actuator also prevents the tail wheel
from swerving during normal landings, or when landing on a sloped terrain, and inhibits shimmy of the tail wheel
during takeoff or landing. The locking pin shears under high side load conditions to prevent damage to the fork,
trailing arm assembly or tailboom. The tail wheel lock actuator system can also be manually controlled. The
handle attached to the lock actuator is used to manually unlock and lock the tail wheel. A quickrelease safety
pin, with an attached warning flag, is used to hold the lock actuator in the unlocked position during ground
handling which prevents accidental locking of the tail wheel. When the handle is placed in the full up position, it
seats the lock pin which secures the wheel in the center position. Placing the handle in the full down position
unseats the lock pin, allowing the fork assembly freedom of movement.
(f) Tail Wheel Proximity Switch.
The working circuit of the tail wheel lock/unlock actuator electrical
operation consists of a TWHL LOCK circuit breaker (CB59) that applies 28 VDC to the pilot TAIL WHEEL
UNLOCK/LOCK switch, to the open contacts of the tail wheel lock relay (K34) and the tail wheel lock proximity
switch. The tail wheel lock relay is controlled by the tail wheel lock proximity switch. When the tail wheel is
unlocked, the proximity switch supplies an electrical ground to the tail wheel lock relay. Placing the TAIL WHEEL
switch in the UNLOCK position applies 28 VDC to the tail wheel lock control valve solenoid allowing hydraulic
pressure to unlock the tail wheel. When the tail wheel lock/unlock actuator is in the the unlock position, the tail
wheel lock proximity switch is actuated and supplies an electrical ground to the tail wheel lock relay. When the tail
wheel lock relay is energized, 28 VDC control voltage is applied to the multichannel dimming controller which
supplies voltage to illuminate the TAIL WHEEL UNLOCK advisory light.
(3) MLG Brake System.
The MLG brake system (fig. 316) provides braking and directional control for
taxiing the aircraft. The brake system holds a maximum alternate gross weight of 17,650 lbs. on a 12 slope. A
separate system is provided for the left and right wheels. The MLG brake system can be operated from the pilot or
CPG station by depressing the top of the pilot or CPG directional control pedals. The parking brake is locked from
the pilot station only, but can be released from either crew station.
(a) Transfer Valves.
The transfer valves allow the pilot or CPG master cylinder pressure to operate
the brakes without mixing fluids. The two transfer valves provide pressure which interconnects between the pilot
and CPG master brake cylinders. The bleed screws on the transfer valve are used to bleed air from the CPG
master cylinders. When the brakes are operated from the pilot station, the transfer valve does not function
mechanically. Fluid pressure passes from the pilots master brake cylinder through the transfer valves to the wheel
brakes. The tranfer valve functions only when the CPGs brakes are operated. Fluid pressure from the CPG
master cylinder moves the piston, opening the CPG inlet port and poppet, thus closing the pilots inlet port which
prevents fluid from flowing back into the pilots reservoir. The CPG piston transmits pressure to the hydraulic fluid
forcing it through the outlet port into the transfer valve. This action operates the MLG wheel brakes. Pressure from
the pilots master cylinder overrides the poppet valve. Unseating the poppet opens the pilots inlet and seals the
CPGs inlet to allow the pilots pressure to operate the wheel brakes.
(b) Wheel Brake Assembly.
The wheel brake assembly converts hydraulic pressure into a retarding
mechanical force that stops wheel rotation. Hydraulic pressure activates three pistons in each brake assembly to
press friction linings against a floating brake disc, thus slowing or stopping wheel rotation.
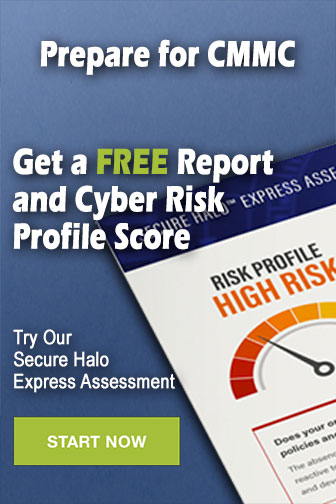